Gone are the days when welding was considered hectic. Human welders have limited capacity; they must be exposed to multiple fumes and radiation, but welding robots have solved all these problems. They are fast, efficient, and can work nonstop without fatigue.
Welding robots have been in the manufacturing industry for several decades, but as manufacturers have been trying to lower costs, they are becoming an essential part of smart production. Overall, robot welding has revolutionized the industry, and they are fast replacing human welders in many industries.
In this article, we will discuss robotic welders. We will give you a brief history and discuss the new future of welding. Before further ado, let’s discuss what Robot welding is:
What Is a Welding Robot?
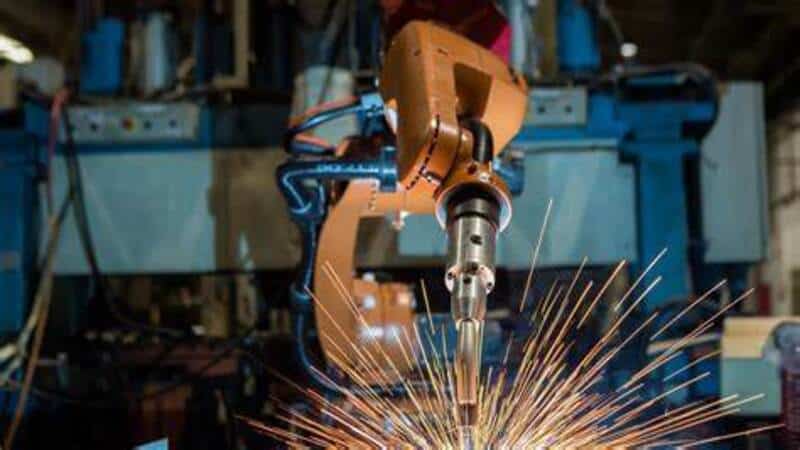
Welding is joining two or more metal materials by melting them. Welding robots are programmable machines that can weld without needing any manual interference. The robotic hands can handle two pieces and enhance the product quality.
Unlike welders, robots can work nonstop without feeling any fatigue or discomfort. It can work in many positions, with fast and precise welding results. A wedding robot can perform several types of weldings with precision.
The History of Welding Robots
Metal fabrication has been a part of human history from the time of caves when tools were made with hands. As time progresses, people learn to melt materials on fire and join them together.
The welding industry has a long history, and Egyptians developed pressure welding as far back as 3000 BC. With time came several welding techniques like arc welding, flux cored welding or MIG welding.
It was until 1962 that the first automated welding attempt was made. A welding robot was used in an automobile company. George Devol and Joseph Engelberger developed The UNIMATE, which was mainly used for spot welding for assembling.
Soon other manufacturers like FANUC, KUKA, and Motoman developed their welding robots, but they were rare due to their high price. Still, manufacturers were working on the robots.
By 2000, welding robots had become more popular in the aerospace, construction, and shipping industries. Nobody doubts the efficiency and advantages of robot welding, but the only hindrance was the high price associated with these robots.
With modern technology evolving, the price of welding robots dropped, and thus, robot welding is becoming more popular in manufacturing industries.
Robotic welding systems continue to boom rapidly, and the latest robots are more technologically advanced. They continue to become more efficient, requiring less and less human involvement. We expect to see them advance as they continue to adapt to more welding processes.
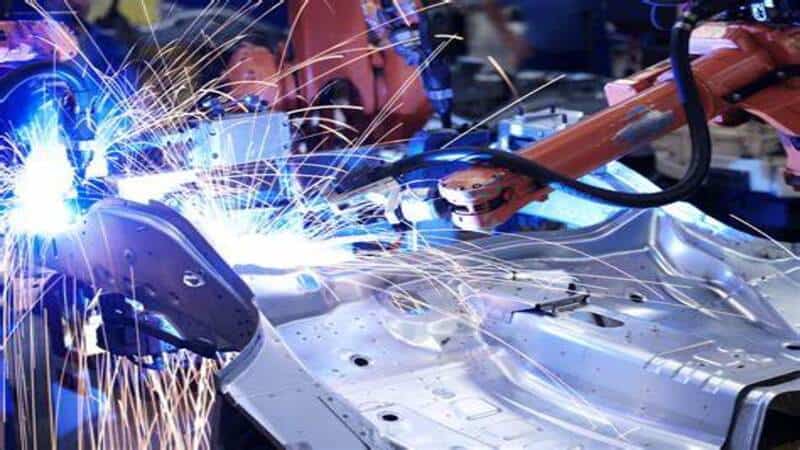
What Are the Types of Welding Robots?
Here are a few types of robot welding technology:
Resistance Spot Welding
Resistance spot welding is commonly used in the automotive industry. Spot welding robots are articulatory robots. These robots have several joints, which makes them versatile and flexible. These robots are used for arc, TIG, or MIG welding.
These spot welding robots have a servo motor with a high-resolution encoder that controls the motion required for spot welding.
Collaborative Robot Welding
Also called Cabot welding, it is designed to work with human welders. They have 6-axis robotic arms that have sensors. These sensors can detect when a human is nearby and slow down or stop when necessary.
Cartesian Robots
These robots have three linear axes that allow them to move in three directions. These robots can be used for manual weldings like arc, MIG, and arc weldings.
SCARA Robot
SCARA robots are designed for precise welding tasks. They are high-speed robots. They have two rotary joints and a vertical axis, which allows them to move in a circular pattern.
Mobile Robot
Mobile robots can be mounted on a mobile base. It allows them to move around a factory floor. These robots are used in shipbuilding or bridge construction where large structures or components are welded.
Gantry Robot
Gantry robots are also used for welding large components. They are commonly used in industries such as aerospace and automotive manufacturing.
Robot Laser Welding
Robot laser welding involves using a laser beam to weld different materials. The robot laser welding machine consists of a fiber laser head, a tracking system, and an industrial robot that can weld material of different thicknesses.
They can work in different directions as well. These robots are used in making medical device components, the aerospace industry, and the automotive industry.
What Are the Applicable Materials of Welding Robots?
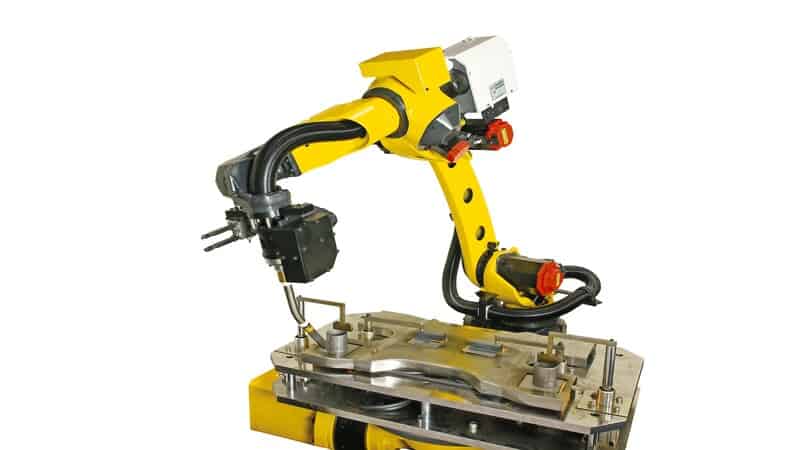
A laser welding robot can work on different thick and thin materials. Their precision lies in handling thick alloys and thin materials that require special care. The highly narrow size of the beam has a small contact zone. Heat affects only the contact zone and does not distort the surrounding material.
This makes them ideal for materials easily distorting or cracking with heat. It does not need any pressure and can weld the thin material with equal precision. The weld seam is also fine and requires little to no post-processing. The strength of welding is also superior to any other type of welding.
Robot laser welding machines can melt and join thick or thin materials and work on challenging materials like aluminum or copper, which are highly reflective. Here are some materials that welding robots can weld. Metals like carbon steel, alloy steel, silicon steel, spring steel, aluminum alloy, or galvanized sheets can be welded with precision and accuracy.
Benefits of Using Welding Robots
Here are a few benefits of using robotic welding systems:
High productivity
Robot welders can weld much faster than any other machine. They can work 80% faster than skilled workers. They work tirelessly without any fatigue and can keep on working all day. These automated welding processes have increased the production output on an assembly line.
Improve Quality
Laser welding robots give consistent quality without any errors. They give high-quality welding in less time and without any manual cost.
Reduce Production cost
Welding robots reduce manual intervention and save production costs. They can work long hours, have better speed, and do not slow down. This increases the productivity of industries and reduces the production cost. They require less staff to monitor or handle the welding process.
Improve Safety
Welding can be dangerous without proper safety measures. The melting process can give off fumes and may be unsafe to breathe. When robots are welding, there is no risk to human life. Robots can perform welding in higher temperatures, fumes, and other hazardous conditions.
Reduce Waste
Laser welding combined with robots gives a new level of accuracy and precision. No material is wasted in this process. The laser beam affects only the zone where it is directed. No material is wasted, and scrap is also minimum. Not only it saves further production costs, but it is environmentally healthy as well.
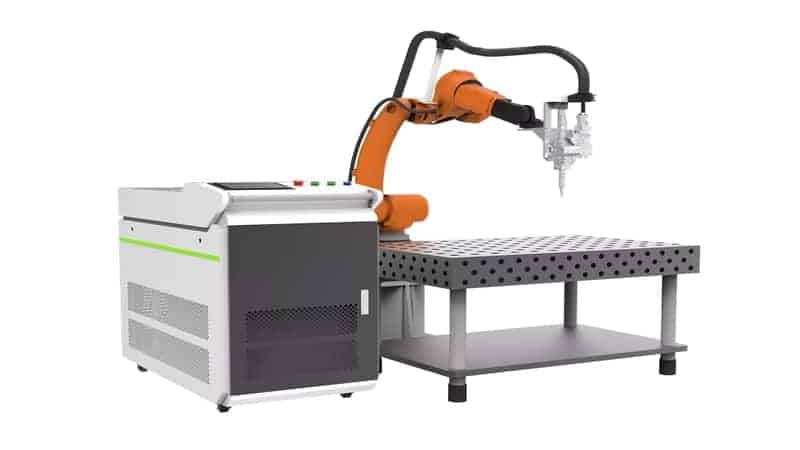
Applications of Robotic Welding
Laser welding robots are versatile and can be used in several manufacturing sectors. Here are a few robotic welding applications.
Automotive Industry
Robot welders are extensively used in automotive industries and manufacturing engineering to build and weld car bodies, engine components, exhaust systems, or other devices and their components.
Aerospace Industries
Laser welding robots give precision that industries like aerospace require for building high-quality turbines, fuel tanks, and other components. It can work on both thick and thin material with equal precision.
Electrical Industry
The electrical industry uses difficult-to-weld materials like silicon, spring, and carbon steel. Laser welding robots can weld components of batteries, sensors, and connectors.
Medical Industry
The medical industry needs components and medical devices like surgical tools, pacemakers, dental implants, and other tools and devices. Laser welding robots have no risk of contamination and give accurate, clean, and precise welds.
Metallurgical industry
Metallurgical industries process and manufacture alloys and metals. It includes extracting metals from ores and shaping them into different forms and materials. Robot welding machines can give control, precision, and consistent quality for repeated welds.
Furniture and Home Appliances
Metal is largely used in the furniture industry. Besides difficult and complex designs, they are used indoors and in windows. Besides, welding is used for cabinets, shelves, and decorative elements. Laser welding robots give clean and strong well to difficult-to-join metals. Modern furniture and home designs require joining several complex shapes that laser welders combine precisely.
Conclusion
Laser welding automation has revolutionized the welding process. They are fast, efficient, and precise. They have a bright future with the latest technology and artificial intelligence. They can increase the production volume while decreasing the production cost to a great degree.
Robots can not only be used for laser welding but they are used for other types of welding as well. As technology progresses, the prices of these robot welding machines are also dropping, making it easier for industries to incorporate them into their production lines.
Revolutionize your Production with Baison’s Laser Welding Robots
Baison offers high-tech welding robots for small to big businesses. Our laser welding robots can perform on complex, thin, or difficult-to-weld materials, giving precise and consistent results. Our laser welding robots can automate your product line and boost production with flexibility, precision, and durability.
Our welding robots have a substantial deposition rate and have streamlined arm designs for maximum access. These robots can perform welding in most hard-to-reach areas where human welders may not perform.
Contact us to learn more about Baison’s laser welding machines. We offer free application evolution and sample proofing to help our clients automate their production lines.