Accuracy and precision are imperative for the welding process. Among the complexities and challenges of this process, welding fixtures offer your support to accomplish your task. They ensure the perfect angle and position of a workpiece during the strenuous welding job. It enables welders to achieve high-quality results.
In this article, we’ll uncover the four types of welding fixtures and their various aspects.
What is a Welding Fixture?
A welding fixture is a uniquely designed tool for the alignment of workpieces and securing them in the right position for laser welding. Its primary purpose is to precisely join the welded components to get quality results. These specialized tools eliminate distortions that can affect the weld. Welded fixtures are made of reliable materials that can withstand heat to ensure long-lasting use.
Various types of welding fixtures are available for different welding processes. Each fixture is specialized for a particular task. However, most of them offer the flexibility to accommodate several welding requirements.
They often incorporate adjustable clamps, supports, and positioning devices for various welding applications. According to the Academia, welding fixtures offer some challenges. One of the major challenges of employing them is to achieve the desired finish to get the required results.
Do You Have Any Questions?
Let Us Solve Your Problem
1 – Modular Welding Fixtures
If you want an all-in-one solution, modular welding fixtures are a fantastic choice for you. These unique fixtures come with various components that you can assemble in your required configuration to achieve the desired results. Their interchangeable nature makes them cost-effective by offering an efficient set up. They enable you to deal with numerous tasks, including welding tiny pieces to complex components.
According to the NASA Technology Transfer Program, NASA’s researchers have created modular welding fixtures to reduce time, labor, and material costs. These unique fixtures address the requirements for various tasks without investing.
The rigid base of the fixture holds the workpiece in place. Various adjustable clamps enable you to position the workpiece. The plates of modular welding fixtures feature a grid, which allows you to adjust and fine-tune the position of each component.
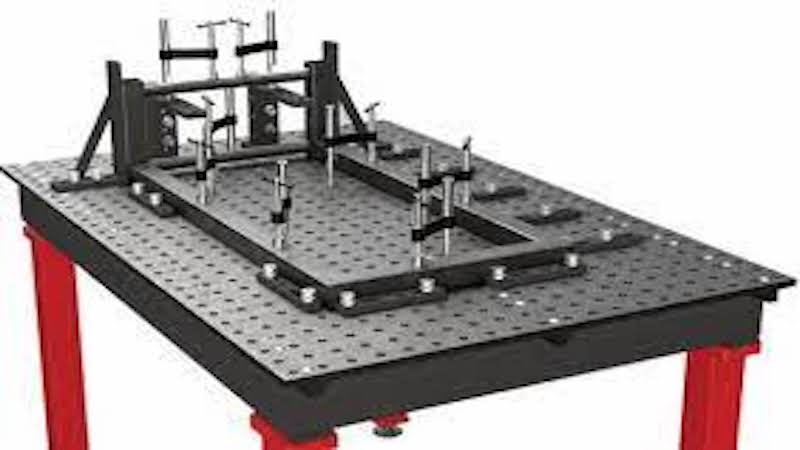
Applications of Modular Welding Fixtures
You can employ these fixtures for multiple projects, making them a cost-effective solution. Here are some of the common applications of modular fixtures:
- In aerospace, precision and reliability are paramount. Modular welding fixtures are used to fabricate critical components such as aircraft frames, landing gear, and engine parts.
- The automotive industry relies heavily on modular welding fixtures for assembling vehicles’ chassis and body structures. These fixtures enable automakers to consistently produce cars with tight tolerances, ensuring safety and quality.
- Shipbuilders employ modular welding fixtures to construct the hulls and superstructures of vessels. These fixtures provide a stable platform for welders to work on, ensuring the ship’s structural integrity.
- Modular fixtures are great options for welders who can’t accommodate various specialized fixtures in their workspace. With modular fixtures, you can efficiently handle diverse welding requirements without taking up excessive space.
- Engineers and researchers utilize modular welding fixtures during the prototyping and testing phases of product development. With these fixtures, you can rapidly create prototypes for various industries. According to the National Conference on Recent Trends in Engineering & Technology, modular welding fixtures can be used for prototyping and temporary replacement.
2 – Dedicated Welding Fixtures
Dedicated welding fixtures are specialized tools used in welding processes to aid in the precise and consistent assembly of components. You can customize the configuration of these fixtures. This feature lets you accurately position the welded components on the table during welding.
The perfect positioning of the workpieces in dedicated fixtures allows you to achieve high-quality welds, especially in industries where accuracy and repeatability are required.
Dedicated welding fixtures aim to stabilize the welded components. They are designed in such an exclusive way that they can secure the position of workpieces with different geometric shapes. It eliminates the need for manual adjustments and minimizes the risk of errors, resulting in welds that meet stringent quality standards.
Moreover, these fixtures can enhance the safety of welding processes by reducing the chances of accidents or injuries caused by unstable workpieces.
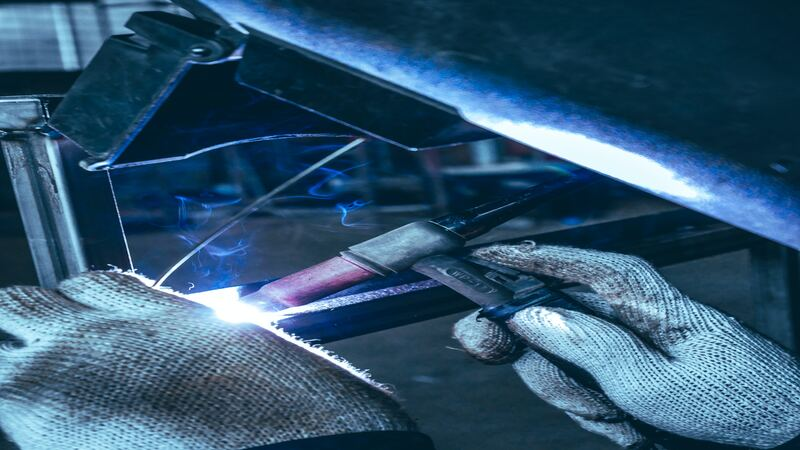
3 – Manual Welding Fixtures
Manual welding fixtures are valuable tools for creating complex or intricate welds. Various factors such as fatigue, inconsistency, and the inherent limitations of the human hand lead to inconsistencies in the weld quality. Manual weld fixtures prevent these issues by providing a stable and controlled environment for welding. They minimize the risks of inaccuracies during welding.
However, you have to align the workpieces on manual fixtures by hand without any assistance. These fixtures are manufactured from rigid materials that can withstand high welding temperatures. They reduce the risks of injuries and improve the weld quality.
Application of Manual Welding Fixtures
The following are some of the common applications of manual welding fixtures:
- Manual fixtures are used in the automotive industry for assembling the components of vehicles. They align the components of automobiles during welding to boost the durability of the weld.
- These fixtures are also employed for repair and maintenance activities. You can use them to fix agricultural machinery and various large components.
- It is also used for the manufacturing of heavy machinery. They help you strongly weld huge parts, resulting in durable and reliable machinery.
4 – Hydraulic and Pneumatic Welding Fixtures
Hydraulic and pneumatic welding fixtures employ pressure in a unique way to hold the workpieces in a fixed position during welding. These fixtures are known for higher precision and repeatability than manual welding fixtures. They also help reduce operator fatigue and boost overall productivity.
a. Hydraulic Welding Fixtures
Hydraulic welding fixtures operate using hydraulic cylinders to clamp the workpiece in the required position. The fluid pressure of the hydraulic system creates a controlled and powerful force. This force is applied through clamps and support structures, ensuring that the workpiece remains immobile during welding. Hydraulic welding fixtures are engineered with precision.
These fixtures allow you to adjust various workpieces. However, this adjustment is limited. These welding fixtures are used in gas tungsten arc welding (GTAW) and gas metal arc welding (GMAW).
b. Pneumatic Welding Fixtures
Pneumatic welding fixtures also utilize pressure in their functions. This type of fixture operates by using compressed air to position the welded parts. They are used for shielded metal arc welding (SMAW) and flux-cored arc welding (FCAW).
The working components of pneumatic welding fixtures include cylinders, valves, and hoses. These components work together to provide you desired clamping force. You can customize these fixtures to hold various sizes and geometric shapes.
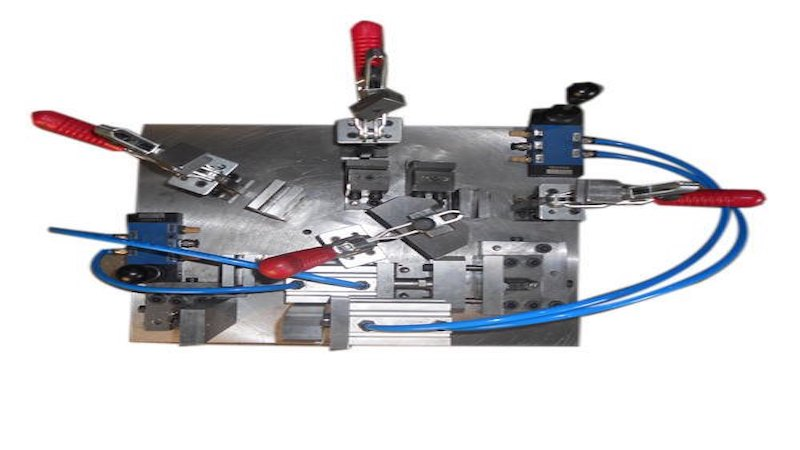
They are designed so that you can change the grip of clamps to minimize damage to workpieces. These features make them suitable for various welding applications, from intricate welding of small components to large-scale industrial welding projects.
Do You Have Any Questions?
Let Us Solve Your Problem
Factors to Consider When Choosing a Welding Fixture
Here are some factors when choosing a good welding fixture for your project:
1. Size and Weight of Workpiece
The dimensions and weight of your workpiece play a crucial role in fixture selection. The fixture must be robust enough to support and securely hold the workpiece during welding without deformation or misalignment. It should also be adjustable to accommodate various workpiece sizes if your projects vary in scale. Robotic welding fixtures are a good choice.
2. Welding Process
The welding method you’ll be using is another critical factor. Most fixtures are designed to support specific welding processes, like MIG welding, stick welding, or TIG welding process. It should provide easy access to the welding area and ensure proper electrode or torch positioning. If you want one solution for various welding processes, a modular welding fixture will work best.
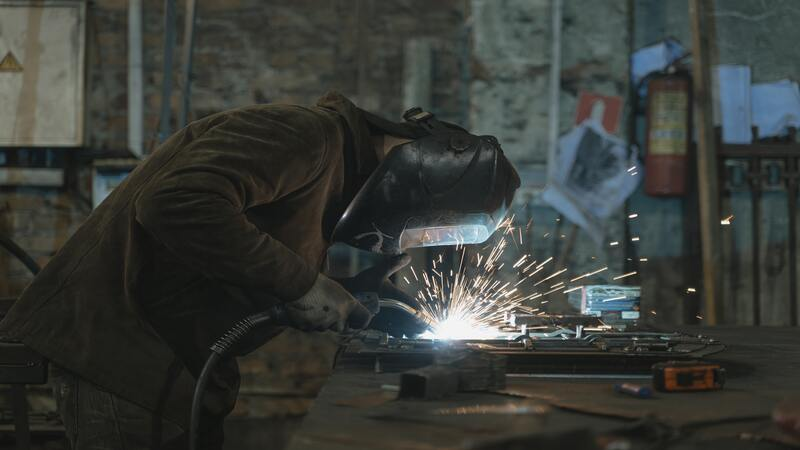
3. Clamping Mechanism
The clamping mechanism is another considerable factor in choosing a welding fixture. It should securely hold the workpiece in place without damaging it. Look for fixtures with adjustable clamps or fixtures that can accommodate a variety of workpiece shapes and sizes.
4. Safety Features
Safety should always be a top priority while working on a welding project. Make sure your welding fixture comes with safety features, such as heat shields or guards. These features protect you from sparks, spatter, and harmful fumes. You should also maintain ventilation during welding.
5. Maintenance and Durability
Durability and maintenance are key features of a welding fixture. Invest in a fixture that is made of durable material and resists rigorous usage. Moreover, pay attention to maintenance requirements. An easy-to-maintain fixture can save you time, allowing you to focus on other tasks.
Do You Have Any Questions?
Let Us Solve Your Problem
Conclusion
Understanding various welding fixtures is necessary to ensure the quality and efficiency of your welding projects. Whether you want a fixture for welding steel structures, automobile parts, or even household items, the four welding fixture types mentioned above will cover your needs. So, after studying the basic principles of welding fixture design, invest in a reliable welding fixture for your next welding project.
Get Great Welding Results With Baison!
Baison Laser offers various laser cutting and welding solutions. Its unique and durable products can cater to all your welding needs. Request an instant quote, and our team of experts will help you select the perfect equipment for your project.