In this article, we break down the role of the bevel cut in laser cutting machines.
What is a Bevel Cut?
A bevel cut is used to create geometrical shapes at the edge of the workpiece by cutting it at an angle. In a normal laser cutter, the edges of the workpiece are at right angles to the face. However, with beveling, the edge becomes non-perpendicular and gets a gentle slope. Most laser cutting machines have a standard slope angle of ±45 degrees.
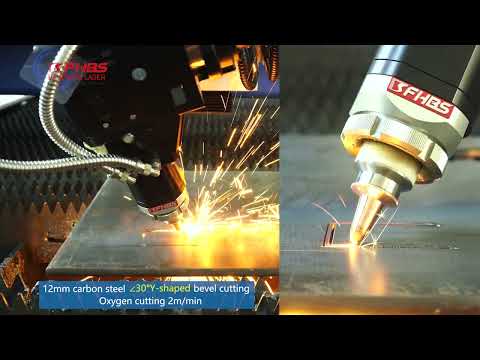
The sharp edges of a freshly cut metal part can be dangerous to handle. So, a bevel cut is employed to smooth the edges and improve worker safety. Beveled edges also improve wear resistance, facilitate smoother welds, and provide better aesthetic purposes.
5 Types of Bevel Cuts
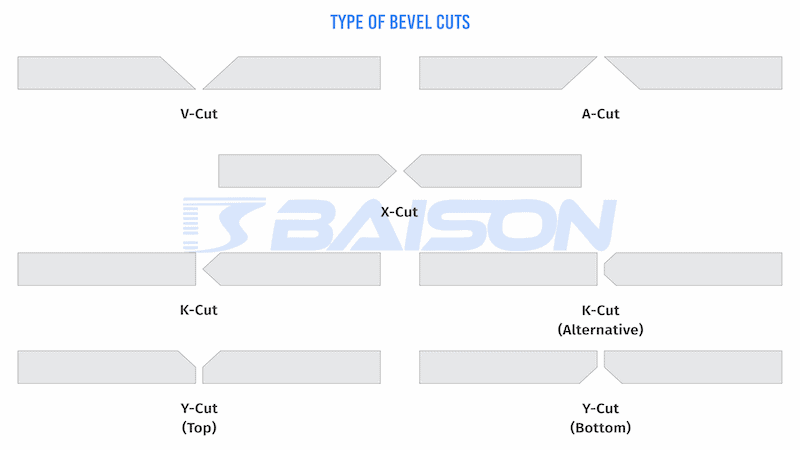
The laser cutter’s angle adjustment control allows operators the freedom to implement various types of bevel cuts. Bevel cuts can be distinguished based on the angle of the blade on machines (laser angle).
The naming of bevel cuts comes from the shape of two adjacent cuts.
1. V Cut (Top Bevel)
The V-cut is the most common type of beveling found in metalwork. Here the laser cuts the workpiece at a set angle, creating a downward slope. When you place two top bevel edges next to one another, it creates a V shape.
2. A Cut (Bottom Bevel)
The A-cut is an inverted V-cut. The workpiece is flipped upside down to get a bottom bevel before fixing it to the laser cutter. In A-cut, the top edge of the workpiece is protruding.
3. X Cut (Top & Bottom Bevel)
Performing a top and bottom bevel on the same edge will give you a wedge shape, also known as an X-cut. With an X-cut, the two bevel cuts meet at the center of the metal plate.
4. Y Cut (Chamfer)
Y-cut is sometimes called a chamfer or chamfered edge. It is similar to a top bevel, except the cut doesn’t reach the end of the plate. A top chamfer is called a top Y-cut, and a bottom chamfer is called a bottom Y-cut.
5. K Cut (Top & Bottom Chamfer)
In the context of chamfer vs. bevel, there are two variations of the K-cut bevels. One is a welding-specific cut with a flat right-angled edge and an X-cut edge. The other is a more general machine cut where the workpiece gets a simultaneous top and bottom chamfer.
Do You Have Any Questions?
Let Us Solve Your Problem
Automated Laser Beveling Cut vs. Compound Miter Saw
Laser bevel-cutting tools are very common nowadays. But before the widespread availability of laser cutters, bevels were cut using traditional methods. You would typically see a combination of circular saw and file used to make bevel cuts.
A compound miter saw is a specialized circular saw with an adjustable blade. Here the saw blade tilts to the desired angle and makes bevel cuts as needed. This system works exceptionally well for small and simple projects. But you can’t rely on basic power tools such as a compound miter saw for larger, more complex designs.
The traditional beveling approach involves cutting the workpiece and then cutting, sanding, or filing beveled edges as part of the post-processing. But with modern automated laser bevel cutting, we can combine these two steps. Laser cutters can be programmed to cut the metal with a beveled edge.
Compound miter saws (circular saws) are advanced forms of old-school hand table saws. They were designed to deal with woodworking projects and fall short when working with metal pieces. The miter saws also lack the high-quality finishing provided by laser cutting tools.
Another shortcoming of the traditional miter saw approach is tool wear. After a few cuts, even a sharp blade will need to be replaced. Contrarily a laser can operate for an indefinite period without wear concerns. Laser bevel cutting is an innovative and efficient improvement to the traditional miter saw approach. It can make an angled cut during the initial cutting process, saving valuable production time.
Miter Cut vs. Bevel Cut
A bevel cut is very similar to a miter cut. In fact, in some cases, both bevel and miter cuts look exactly the same. The confusion comes from the terminology used for the two types of cuts. A 45° miter cut means the cut angle is 45° on the surface of the metal plate. While a 45° bevel cut means the cut angle is 45° along the thickness of the metal plate.
A miter cut only has one miter angle. But a bevel cut can have a miter angle and its bevel angle.
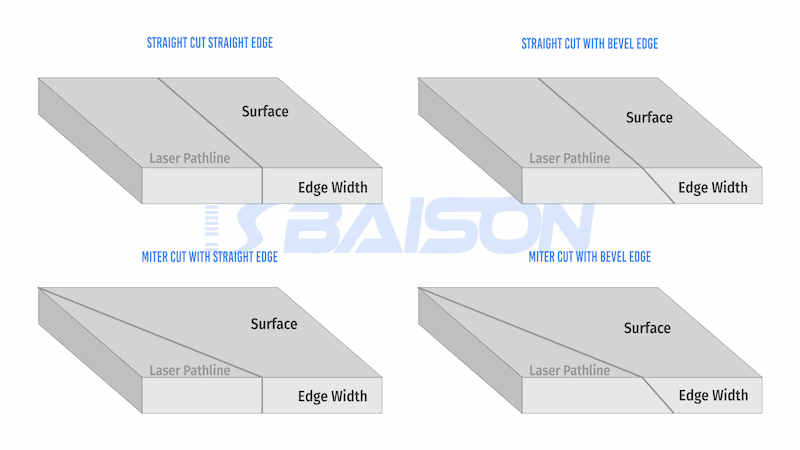
The picture above shows the subtle difference between the miter cut and the bevel cut. The edge width of the workpiece defines bevel cuts. In comparison, a miter cut is defined by the surface of the workpiece.
Miter cuts with a beveled edge can be made using a circular or table saw. Almost every circular saw nowadays comes with tilt adjust capabilities. However, it should be noted that laser cutters can make miter cuts faster and more precisely than any circular or table saw.
Do You Have Any Questions?
Let Us Solve Your Problem
Applications of Laser Bevel Cuts
A laser beveling machine is versatile and can be deployed for several applications. Because at its core, laser beveling is a regular laser cutter with an additional axis of rotation. The laser can move in three axes (x, y, and z) and pivot along the z-axis.
1. On Machine Countersinking
Countersinking makes a bevel (conical) hole on top of a screw or rive hole. The purpose of a countersink is to keep the screw flush with the surface of the metal.
Traditional manufacturing involves cutting a metal part, removing it from the machine bed, and taking it to another machine, such as a drill press. This is an off-machine process, as the workpiece needs to be taken off the machine to perform beveling.
On the machine means the workpiece, after being cut, can be beveled on the same machine bed. Laser beveling machines can perform countersink operations on the machine during the cutting process.
2. On Machine Chamfering
Chamfering makes angled cuts to smooth out the sharp edges of a square cut. It is both a bevel cut and a finishing process. Angle cut operations are convenient with laser cutters and exponentially faster than traditional methods.
Chamfering is a basic finishing process commonly used to remove machining burrs from the edges. This process can be performed fairly quickly using manual tools. Having the convenience of a fully automated laser cutter makes the process even faster.
3. Weld Preparation
Another big advantage of bevel cuts lies in weld preparation. The above-mentioned A and V- -cuts are designed to improve weld efficacy. Bevels increase the weld surface area of two adjacent workpieces and provide a basis for a stronger bond.
Weld preparation and chamfering are the two most popular use cases of laser bevel cutting.
4. Cutting Oddly Shaped Parts
The operator’s imagination only limits angled laser cutting. Adding another axis of rotation to a cutting machine will allow more diverse cutting operations. Undercuts and conical cuts are very difficult with regular laser cutters.
There are workarounds to help you make complex cuts with regular laser cutting machines. But they have their limitation. For example, you can make normal cuts on the first pass and reorient the workpiece to make angled cuts on the second pass.
The set path of the laser beam on the metal surface is called a pass. Lasers can’t penetrate thicker materials, so they are cut in multiple passes. Multi-pass cutting is a very time-consuming process. It takes more time to remove and reorient the workpiece than to perform the cutting operations.
Thus, automated laser beveling is the way for complex designs requiring straight-edge and angled cuts. Its on-machine processing is a major time saver and keeps high-volume productions on track.
Do You Have Any Questions?
Let Us Solve Your Problem
Conclusion
Bevel cuts are a very important part of modern laser cutting. It allows for more versatile manufacturing techniques to be deployed by operators in a short time. Laser bevel cutting has two distinct advantages over traditional methods, on-machine beveling, and automated computer-controlled operations. And because of that fiber laser cutting is the future.
Get a Laser Cutting Machine from Baison!
Baison is a leading manufacturer of high-quality and durable fiber laser systems. Our unwavering excellence has allowed us to support thousands of businesses in over a hundred countries and regions. Our stacked product catalog has a fiber laser machine for every application.
Experience our best-in-class customer service and get an Instant Quote Now!