Welding is an essential process in many manufacturing industries, and the decision to use either handheld or robotic welding machines significantly impacts your production process and the quality of the welds. Handheld welding machines are portable and cost-effective, while automated welding robots can perform larger, more complex tasks.
In this blog post, we’ll compare and contrast these two welding machines using their benefits, drawbacks, and factors you should consider when choosing between them.
Whether you’re a professional or newbie to the industry, our comprehensive overview of these welding machines will help you make an informed decision as applicable to your manufacturing process.
What Is a Handheld Welding Machine?
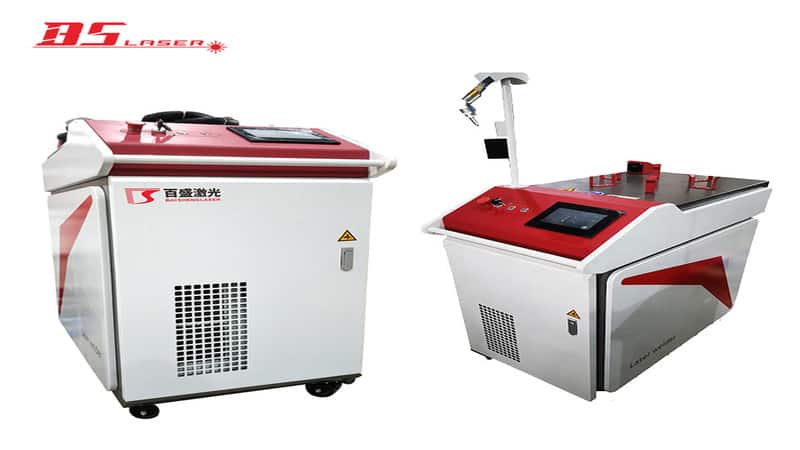
A handheld welding machine is a portable laser welding equipment that uses fiber lasers to perform non-contact welding techniques. This form of manual welding uses high-power, continuous, or pulsed laser beams to melt and bind metal together.
These machines are small, lightweight, and portable and primarily used in industries requiring precision and long-distance welding. They also require reduced heat input, making them more environmentally friendly than traditional welding machines.
Click the button below to get a professional handheld welding machine.
Benefits of Using a Handheld Welding Machine
Portability
Portability is one of the significant advantages of handheld over traditional welding machines. Handheld welding machines are typically designed to be small and lightweight, allowing human welders to transport and operate them efficiently in various locations.
Some of these laser welding machines even come with rechargeable batteries, further adding to their portability and allowing them to be used in remote locations lacking electricity. Their portability prevents you from having to transport heavy metal materials to and from your work site.
Versatility
The versatility of these handheld welding equipment is unmatched, as they can be used for a wide range of welding projects. These machines have applications in different industries, such as automotive, manufacturing, medical, aerospace, jewelry, and art.
They are also designed to efficiently mold different shapes, thicknesses, and sizes of materials like stainless steel, aluminum, and brass. However, asides from welding, these machines can be used in these industries for drilling, marking, and cutting of metals.
Cost-Effective
Handheld laser welding equipment might be a bit pricey when purchasing. Still, they become affordable and cost-effective for your business in the long run, especially if you’re into high-volume production.
This is due to the aggregate of other benefits, such as reduced welding time and labor costs and increased output for better mass production. They also eliminate the need for additional welding equipment and finishing touches after welding, like polishing or grinding, thereby saving time and resources.
Easy to Use
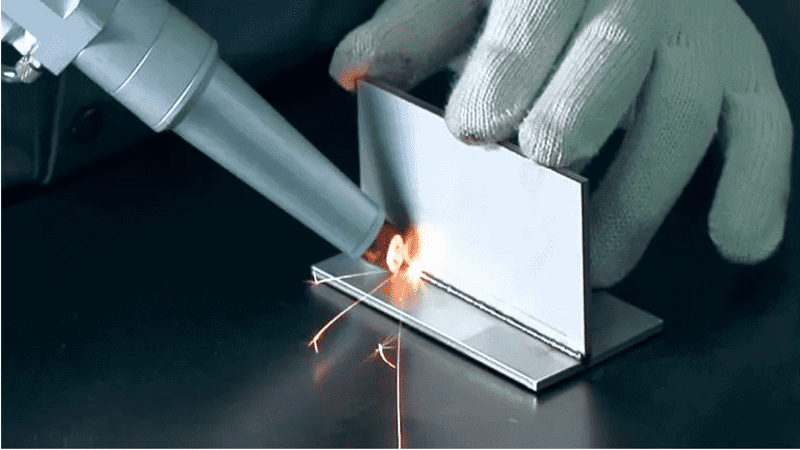
Handheld welding machines are easy to use but require some training and skill to operate efficiently. These machines require you to have good coordination and a steady hand, depending on the magnitude of the welding process.
Additionally, human welders must wear protective gear when operating these machines. However, most handheld laser welding machines are designed with user-friendly interfaces, allowing users to adjust settings and detect errors easily while working.
Energy Efficiency
Handheld laser welding equipment requires less energy than traditional ones to operate. This is because their high-efficiency fiber lasers are used to join various components that use less energy and produce fewer emissions.
These machines also allow fewer materials to be used in welding processes since they offer better precision. This, in turn, reduces the amount of waste generated and material costs.
If you are interested in some common handheld welding Problems, click the button below!
What Is a Welding Robot?
A welding robot is a programmable automated welding machine performing specific tasks. The robot can perform fully automatic or semi-automatic welding processes and is best suited for high-volume productions. These robotic welding systems typically consist of a welding gun, robotic welding software, sensors, a robotic arm, a controller, and a power supply.
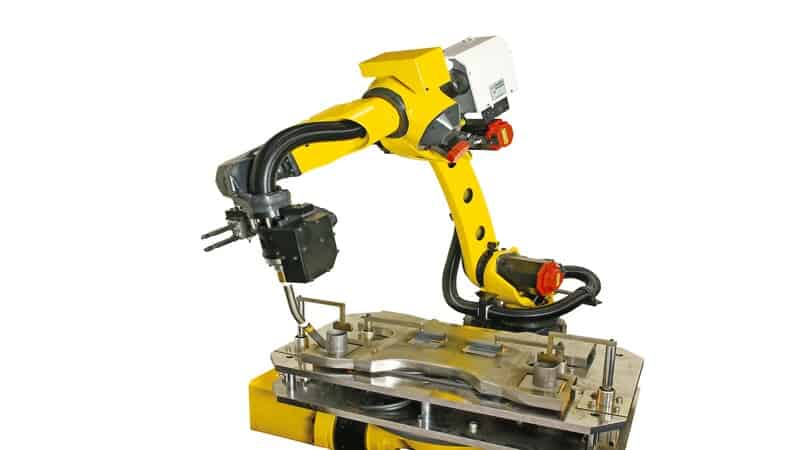
Benefits of Using Welding Robots
Efficiency
Robotic systems can complete an entire welding process at steady and faster speeds and in shorter times than manual welders. They are designed to achieve high precision with fewer errors-a feat that can be challenging for human welders, so factors that can lead to loss of accuracy or reduced output, such as fatigue, distractions, and injury, are eliminated.
Accuracy
Welding robots are highly accurate and precise due to their advanced programming systems, producing deep, cleaner welds that require little to no finishing work. These systems position the laser beams efficiently to ensure highly accurate cuts and mold.
Robotic welders are also designed to monitor the weld quality in real-time, ensuring corrections are made to produce high-quality welds and accurate results.
Safety
When used correctly with appropriate safety measures put in place, robot welders are generally safe. Since these machines are almost always fully automated, they can perform the same tasks as qualified welders without suffering fatigue, distractions, or sickness that causes injuries.
Furthermore, these welding robots reduce the risk of injury by performing hazardous tasks or working in risky locations that manual workers cannot. They also reduce human exposure to radiation and harmful emissions and aid your company’s compliance with safety regulations, thereby improving workplace safety.
Consistency
Once programmed, robotic welders can perform the same tasks routinely without error, generating the same results over a long period. They can repeatedly accurately position the laser beam to achieve the same final results.
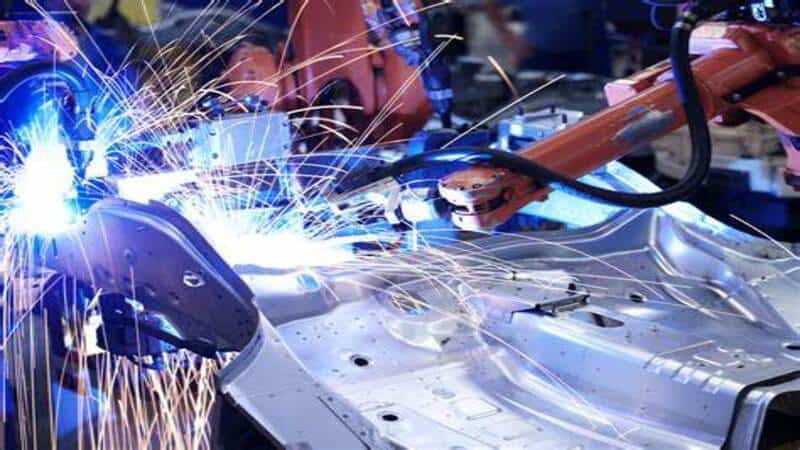
Flexibility
Welding robots are flexible and versatile. You can customize them to meet different manufacturing and production demands, performing a wide range of welding jobs such as contour and spot welding.
You can also apply them in welding other materials apart from metal, such as plastics and composites or implants in the medical industry. You can also create a fully-automated chain of production by integrating your welding robots with other automated systems.
Affordability
Since robotic welding requires fewer workers to perform tasks, it reduces labor costs such as lunchtime breaks, injury, overtime pay, staff turnover, and sick leaves while increasing uptime and efficiency.
It also allows you to cut down on production costs since it can operate day long without fatigue. By using robotic welders in your production process, you can reduce the amount of waste generated and save costs on materials since they only use the necessary materials.
What Are the Differences between Handheld Welding Machines and Welding Robots?
Automation
Handheld Welding Machines: Must be manually operated by a human user.
Welding Robots: Ability to carry out welding processes without human usage.
Precision
Handheld Welding Machines: Precision is limited due to factors that can cause flaws, such as fatigue or human error.
Welding Robots: Robotic welders can perform welding tasks with increased precision and accuracy.
Cost
Handheld Welding Machines: Initial costs for purchasing and maintenance is more affordable than robotic welders.
Welding Robots: Initial purchasing, installation, and maintenance costs for a robotic welding system are high but help to save money on production costs in the long run.
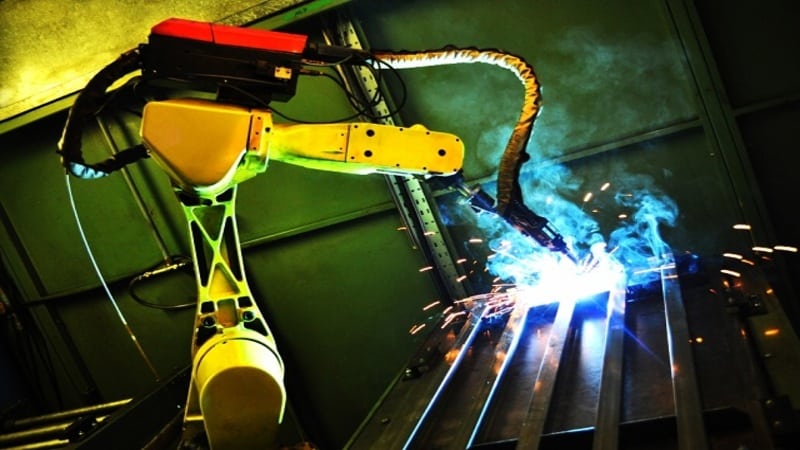
Welding Quality
Handheld Welding Machines: Can be operated by skilled welders to produce polished, high-quality results with attention to detail.
Welding Robots: Maintain weld integrity and achieve higher accuracy with little to no errors.
Safety
Handheld Welding Machines: Employees can sustain injuries while operating these machines.
Welding Robots: Can perform risky tasks and guarantee employee safety.
Flexibility Handheld
Welding Machines: Human workers can perform tasks once they understand the procedures.
Welding Robots: Requires you to reprogram the system every time there is a new project.
Which One Is Right for You?
To successfully determine which laser welding system best suits your needs, it is helpful to review certain factors in order to stay competitive in the market. The first and most realistic factor is cost. If your business can afford to purchase, install, and maintain a robotic welder, go for it. Otherwise, staying within budget and getting a handheld welding machine will be best.
It would also help to consider the magnitude of the production you want to carry out. Robotic welders are mostly cost-effective for large-scale productions. But ultimately, the precision level, speed, and flexibility of welding projects you are doing will determine which system will help you achieve the desired outcome for your business goals.
Conclusion
Summarily, you should take the time to weigh the pros and cons of each welding machine to ensure you are selecting the right one for your business needs. Consider factors such as precision, safety, accuracy, cost, ease of use, efficiency, and versatility. But ultimately, your decision should be based on the magnitude of your production, product quality, and expected return on investment.
You can explore other helpful resources on our website for more information and further understanding of how these welding machines can benefit your business.
Discover the Perfect Solution for Your Business with Baison
Are you an experienced professional looking to upgrade your equipment for increased productivity? Or a small business owner looking to stay up-to-date with the latest innovations in the manufacturing industry? You’ve come to the right place. Elevate your business’s scalability and product quality with cutting-edge laser welding machines from Baison.
Don’t hesitate to click the button below to contact us!