Laser cutting and metal stamping are two popular methods of cutting metal, each with its own advantages and disadvantages. Knowing the base working principles of these techniques is a crucial step for upcoming entrepreneurs.
This article compares and contrasts these techniques, discussing their benefits and drawbacks to determine which metal-cutting machine is best for your business.
What is Laser Cutting?
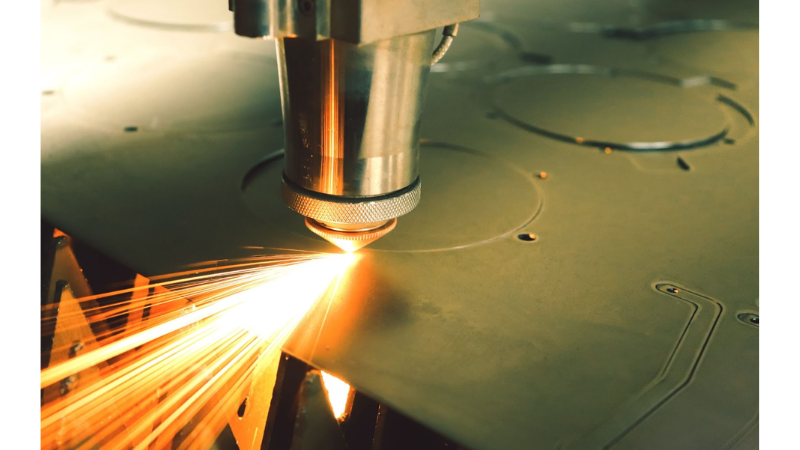
Laser cutting is the process of using a powerful laser beam to make precision cuts into a sheet of metal. The laser beam is controlled by a computerized motor system that follows a pre-programmed path.
The electricity consumption of the laser system defines the cutting power of a laser cutting machine. Low-power cardboard cutters start at 5W, and industrial metal plate cutters can exceed 10kW.
Types of Laser Cutting Machines
Laser cutters are primarily categorized based on the underlying laser technology. The most common types of laser cutting machines are as follows.
- Fiber Laser Cutting Machine
- CO2 (Gas) Laser Cutting Machine
- Neodymium (Nd) Laser Cutting Machine
- Diode Laser Cutting Machine
Laser Cutting Process
The laser-cutting process generally remains the same across all machines. First high-voltage electricity into visible light. This system can be a diode for fiber laser metal cutters or a glass tube for CO2.
Next, the visible light passes through a gain medium to increase strength and transform into a laser beam. Once the laser beam reaches the desired intensity, it leaves the gain medium through the laser head.
The laser head is a computer-controlled (CNC) exit node that moves across the work surface as it cuts through the workpiece. Lasers have a very small contact point called a spot diameter, which ranges from 0.003 in. to 0.007 in.
Some laser-cutting machines output over 1000W of energy through this small contact point, instantaneously melting the workpiece before any warping or cracking can occur.
The cutting process takes only a few seconds to complete. The following parts are about the pros and cons of laser cutting.
Benefits of Laser Cutting
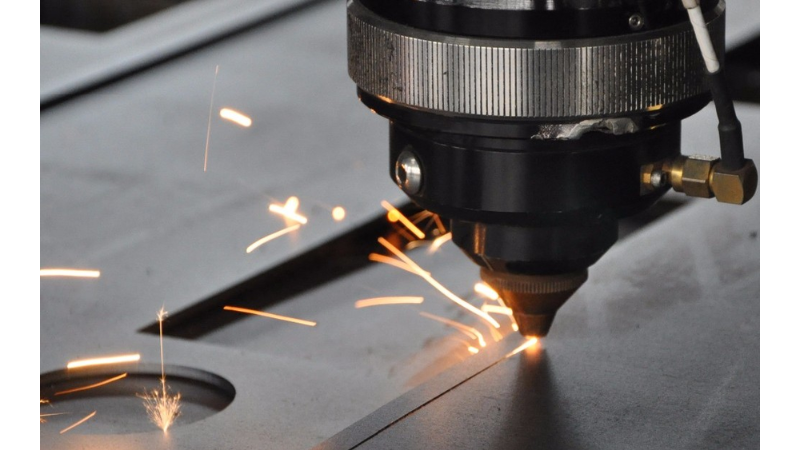
Here is a short list of the biggest benefits laser cutting brings to metal fabrication.
1. Precise Laser Cutting
As everything is computer-controlled, laser metal cutters can repeatedly reproduce parts with exact dimensions and zero practical variance.
2. Quick Processing
A laser cutter can quickly cut through most materials, and the cutting speed can be further increased when processing thinner workpieces.
3. Zero Mechanical Stress
The laser-cutting process selectively cuts through metals by melting them. Since no mechanical force is applied to the workpiece, internal stresses don’t build up in the metal.
4. Accurate Edges
The excellent precision of laser cutting machines allows you to cut complicated shapes with small sharp edges that would otherwise be impossible with traditional manufacturing.
5. Reduced Tool Wear
Lasers don’t have any mechanical wear and tear. Thus they can continuously cut through metals without needing a tool change. Lasers only need to be replaced once their lifespan reaches its limits.
6. Little Post-Processing Required
Lasers produce smooth edges with zero burrs on the workpiece. Hence there is little need for post-process clean-up techniques.
7. No Additional Equipment
Compared to metal stamping, laser-cut parts do not require additional equipment like dies.
8. Material Compatibility
Most laser Cutters are designed for metal fabrication but maintain reasonable compatibility with non-metals like wood, fabrics, and plastics.
9. Versatility
Material penetration of a laser is reduced when the input power is decreased, or the laser beam is out of focus. Modern laser cutters use low-power modes and unfocused beams to switch to an engraving mode.
Cons of Laser Cutting
Following is a list of shortcomings inherent to laser cutters.
1. Temperature Damage
Exposing certain metals to high temperatures can cause unwanted warping, burning, and melting. Thin metals like copper and volatile ones like magnesium require extra care and precautions when laser cutting.
2. Material Compatibility
Laser cutting supports both metal and non-metal materials. However, the material support can be very confusing for newcomers.
Only neodymium (Nd: YAG) lasers support ceramic cutting, diode lasers have better support for fabrics and leather, CO2 lasers are more suited to rubber and plastics, and fiber lasers are better at cutting metals with reflective surfaces.
3. Cutting Depth Limitations
Laser cutting is best suited to thin metal sheets. Cutting a particular part out of thicker sheets is possible. Still, it requires additional power and slower speed, which can often result in unwanted melting around the freshly cut edges of the workpiece.
4. Inability to Bend Metal
Metal stamping at reduced power will result in metal bending. Laser machines are incapable of such metal manipulation.
What is Metal Stamping?
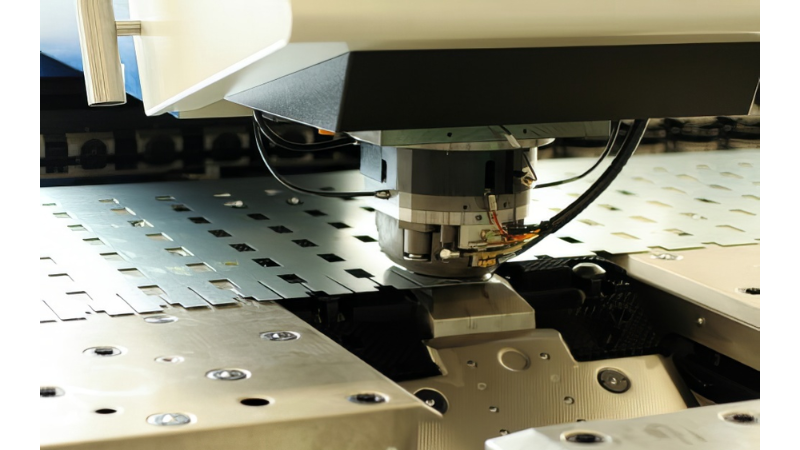
Metal stamping is a metal forming process that uses a punch and die combo to cut metals. The sheet metal is sandwiched between a bottom die and a top punch.
A hydraulic system quickly and precisely applies several tons of pressure on the punch as it is pushed into the workpiece to create the desired shape.
This process allows the operator to quickly stamp (cut) out several hundred shapes from the metal in a single run. Some machines utilize multiple dies to produce more parts with a single stamping press stroke.
Metal Stamping Process
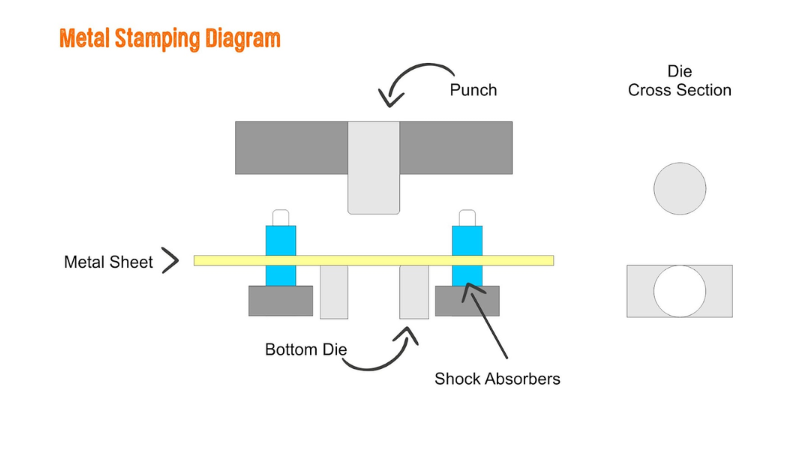
Metal stamping is a simple process that follows the same general steps regardless of machine size. A metal dies and punch are created from high-strength tool steel. The die is fixed to the workbench, and the punch is fixed to the piston.
The die cross-section shares the same design as the desired shape. Meanwhile, the punch shape is the geometric inverse of the die.
Stamping can start once the sheet metal is loaded into the machine. Smaller machines can only load one small metal sheet at a time. But a larger stamping machine requires a roll of metal to be continuously fed to it.
The machine applies enough force onto the punch to push it through the steel metal until it makes contact with the die underneath, shearing the metal at the edges.
Additionally, automatic stamping machines apply force in set intervals timed according to the metal feed rate. Allowing you to cut thousands of parts from the same sheet roll in one long continuous cycle.
Benefits of Metal Stamping
1. Cost Effective
The only costly component of this process is the dies. Hence the cost is higher with the initial units produced. But starts to drop off as the number of units increases. Factories will use one die for over a hundred thousand stampings before replacing the tool.
2. Faster Large Volume Production
A metal stamping machine will continuously run as long as the sheet metal is fed. Large-scale factories can produce close to a million parts using this process. Metal stamping is a great option for repetitive production.
3. Broad Metal Compatibility
Some metals can react negatively to the heat from lasers. Weak metals can melt and warp, while volatile ones like magnesium can ignite. Since metal stamping only applies mechanical force, the risk of material damage is negligible.
4. Versatile Operations
Metal stamping can do a lot more than cut holes. It can perform secondary operations like edge flattening, coin metal forming, metal engraving, and more. A press brake can be added to a metal stamper for additional bending capabilities.
Cons of Metal Stamping
The metal stamping process is generally the best option for large-volume productions. Outside of this specific process, it can run into several limitations.
1. Higher Cost at Low Volumes
Metal stamping jobs require new dies with every new design iteration. These dies are expensive, making the process less profitable for smaller-volume production.
2. Limited Compatibility with Soft Metals
If the working material is a soft (malleable) metal, it will bend under pressure instead of cutting.
3. Limited Compatibility with Harder Metals
Harder metals are very tough to process and can easily crack under high pressures. Hence, you must first stamp out your designs and then harden them using annealing.
4. Structural Weaknesses
Bending metals using the metal stamping process will create structural weaknesses in the workpiece in the form of microscopic fractures.
5. Tool Wear
Physical tooling will always require more maintenance. As the tool repeatedly brushes against the metal workpiece will start to degrade. Harder workpieces will result in faster tool wear.
6. Post Processing
Metal stamping requires post-process cleaning and heat treatment to remove sharp edges and stress marks.
Laser Cutting vs. Metal Stamping: How to Choose?
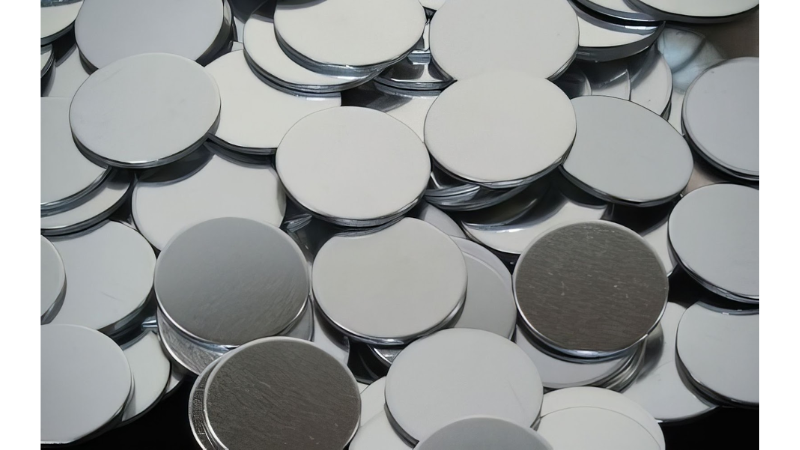
Laser cutting and metal stamping are two very different processes with overlapping applications. Here is a quick comparison for easy understanding.
Features | Laser Cutting | Metal Stamping |
Operations | Cutting & Engraving | Cutting & Bending |
Tool Wear | Very Low | Low |
Material Compatibility | Very Good | Good |
Precision | Very High | Medium |
Upfront Cost | High | Medium to High |
Additional Costs | None | Tool Costs |
Operational Costs | Low at Small Volumes | Very Low at Large Volumes |
Post Processing Costs | Very Low | Medium to High |
The choice between a metal stamper and a laser cutter comes down to one of the many factors listed below. Consider these things for a better solution.
- Applications – Large-volume productions, thicker metal plates, and metal bending are all best suited for stamping.
- Sheet Thickness – Lasers are better suited for soft metal under 15mm and steel sheets under 6mm.
- Material Compatibility – Laser cutting machines have better overall material compatibility. Read the blog to learn what materials can a fiber laser machine cut.
- Process Capabilities – Lasers are better suited for complex geometry designs.
- Upfront Cost – Both machines have a similar upfront cost. But the need for a custom die results in a much higher upfront cost.
- Maintenance Cost – All the cost savings you gain from large-volume metal stamping are lost to tool wear. Replacement costs for tool dies are not cheap and especially for complex geometries.
- Lead Time – Laser cutting has shorter lead times when dealing with small productions, and stamping has better lead times for larger ones.
Conclusion
Laser cutting and metal stamping are the two methods commonly associated with sheet metal fabrication. Laser cutting is more suited to smaller batches of customized parts. While stamping excels at large-volume factory productions.
Other factors like cost savings and material compatibility are generally considered secondary. At the end of the day, your choice of sheet metal fabrication machine is more dependent on the type of business you run.
Maximize Production Potential with Our Metal Cutting Machines
Baison Laser is a top-tier fiber laser systems manufacturer from China. We have delivered the best in class products to over 100 countries in the last two decades.
Our unmatched experience and unwavering dedication to excellence have led to our reputation as a trustworthy and reliable company.
Baison also offers free in-depth evaluation where our laser-cutting experts assess your business needs and applications and pair you with a laser machine that will maximize your production potential.
So you will always get a machine best suited for your needs. Get a Free Application Evaluation Today!