This blog post aims to provide a comprehensive overview of these laser welding techniques. Moreover, we will highlight their respective advantages and drawbacks. By the end of this post, you’ll know how to choose the most suitable laser welding method for your business, ensuring optimal results and efficiency.
What Is Laser Welding?
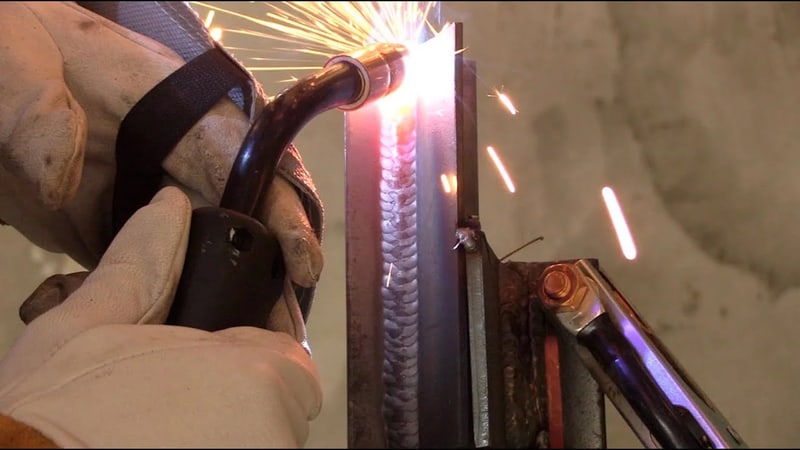
Laser welding is a cutting-edge manufacturing process that utilizes concentrated high-power laser beams to join materials, primarily metals. The high-energy laser beam heats the material, causing it to melt and form a weld pool. A robust, high-quality joint is created as the weld pool cools and solidifies.
This technique offers exceptional precision, minimal heat input, and reduced distortion, making it ideal for various industries. You can learn more about the advantages and disadvantages of laser welding.
Moreover, laser diode welding enables faster processing speeds and increased productivity. On top of it, it’s highly adaptable, catering to various applications ranging from automotive and aerospace to medical and electronics.
Additionally, with the growing demand for precise and efficient manufacturing processes, laser welding has become an indispensable tool for many businesses.
What Are the Common Laser Welding Materials?
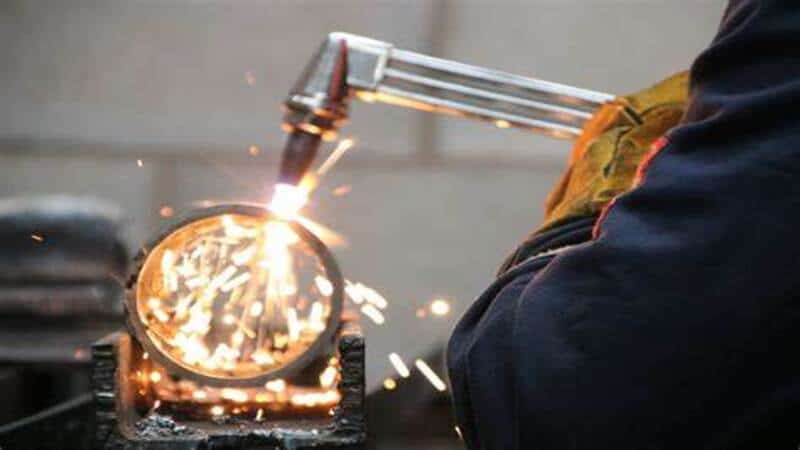
Laser welding works effectively with various materials, making it an ideal choice for several industries. Some common materials used in laser welding include:
1. Steel: Widely employed in the automotive industry for car body panels and structural components. Moreover, heavy industry and transport also laser weld steel for constructing equipment, railroads, and industrial machinery.
2. Aluminum: Utilized in the automotive and shipbuilding industries, aluminum is a popular choice for lightweight designs, especially in car parts and ship structures such as hulls and frames.
3. Stainless Steel: A go-to material for appliance manufacturing and oil and gas industries. Stainless steel is used in household appliances like washing machines, refrigerators, pipes, valves, and other components in oil and gas operations. Often seam welding helps with these tasks.
4. Corrosion-Resistant Alloys: Essential for the oil and gas industry, these alloys ensure safe and efficient operation in harsh environments. Additionally, they have high durability and resilience.
5. Various Metals: In rapid manufacturing industries like aerospace and electronics, laser welding can join a range of metals to create complex, high-precision parts quickly and accurately.
What Is CW Laser Welding?
CW laser welding, or Continuous Wave laser welding, is a technique of spot welding where the laser beam remains continuous during welding. As a result, manufacturers are able to achieve highly smooth and consistent joints. How does this happen? The continuous wave laser output generates a stable weld pool which aids this.
In CW laser welding, the heat input and penetration depth can be controlled by adjusting the laser power and speed. This method is particularly suitable for applications that require deep penetration and high welding speeds, such as automotive, shipbuilding, and heavy industries.
Moreover, the continuous wave nature of the process allows for the efficient joining of large metal components and thick materials, resulting in durable and high-quality connections. Hence, CW lasers come in really handy for businesses.
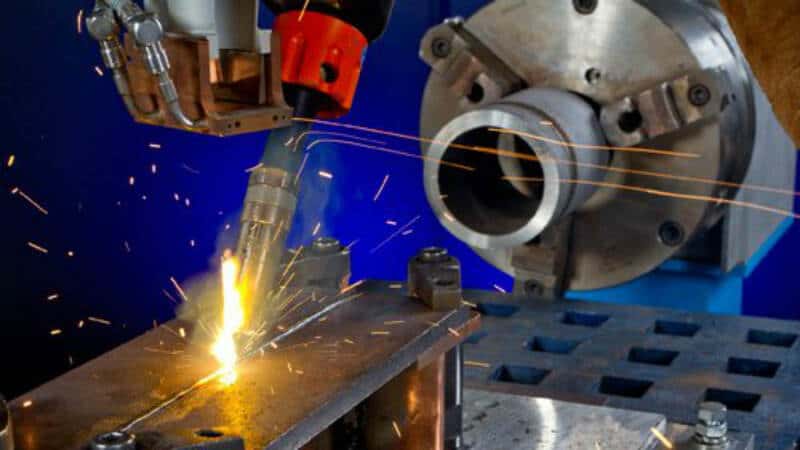
What Is Pulsed Laser Welding?
Pulsed laser welding is an example of a technique that utilizes intermittent laser pulses instead of a continuous wave beam. The laser emits energy in short bursts, allowing precise control over the heat input and minimizing the risk of material distortion or damage risk.
The pulsed nature of this method makes it ideal for thin or heat-sensitive materials, often found in industries like electronics, medical devices, and aerospace. By adjusting the pulse duration, frequency, and peak power, operators can optimize the welding process for specific applications.
Additionally, pulsed laser welding provides excellent results. These include minimal warping and extremely good precision. As a result, it becomes a popular choice for intricate and delicate assemblies. This is true even for high heat-affected zones.
What Is Modulated Laser Welding?
Modulated laser welding is a technique that typically involves altering the laser beam’s intensity, frequency, or duty cycle during the welding process. This modulation allows for precise control over the heat input, ensuring optimal results based on the material and application.
This type of laser welding does a great job of finding the right balance between the laser speeds, heat input, and depth of penetration. Hence, this adaptability makes it suitable for a wide range of industries and materials, from thin, heat-sensitive components to thicker, more robust parts.
Furthermore, the ability to control the laser’s parameters in real-time results in enhanced welding quality, reduced heat-affected zones and minimized distortion. This helps deliver high-performance fiber lasers and connections tailored to specific requirements.
Differences between CW, Pulsed, and Modulated Laser
This table summarizes the core differences between Continuous Wave, Pulsed, and Modulated Laser Welding, highlighting their unique characteristics, which make them suitable for different applications and industries:
Parameter | CW Laser Welding | Pulsed Laser Welding | Modulated Laser Welding |
Beam Type | Continuous | Intermittent Pulses | Variable Intensity |
Heat Input | Constant, High | Controlled, Low | Precisely Adjustable |
Penetration Depth | Deep | Shallow | Adjustable |
Welding Speed | High | Moderate | Adaptable |
Material Thickness | Thick Materials | Thin Materials | Versatile, All Thicknesses |
Industry Suitability | Automotive, Shipbuilding, Heavy | Electronics, Medical, Aerospace | Wide Range of Industries |
Distortion | Moderate | Minimal | Minimized |
Heat-Affected Zone | Larger | Smaller | Reduced |
Advantages and Disadvantages of CW, Pulsed, and Modulated Laser Welding
Here are the advantages and disadvantages of each type of laser welding listed in the points:
Continuous Wave Laser Welding
Advantages:
- High welding speeds
- Deep penetration
- Suitable for thick materials
- Ideal for automotive, shipbuilding, and heavy industries
Disadvantages:
- Constant high heat input
- Greater risk of distortion
- Larger heat-affected zone
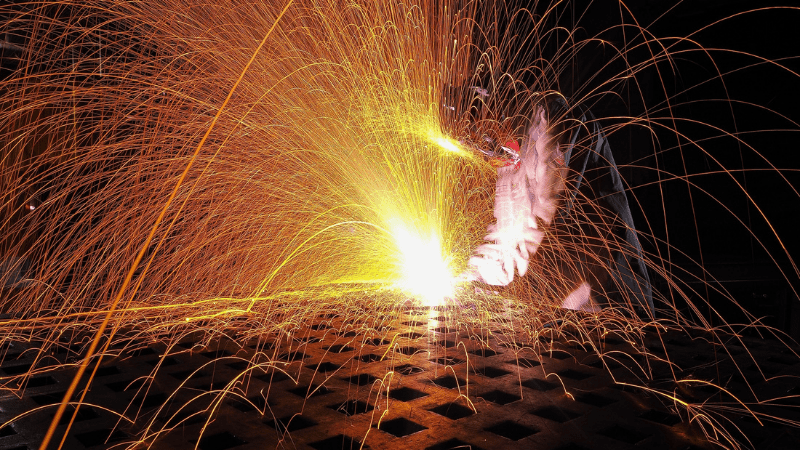
Pulsed Laser Welding
Advantages:
- Precise control over heat input
- Minimal distortion
- Reduced heat-affected zone
- Ideal for thin and heat-sensitive materials
- Suitable for electronics, medical devices, and aerospace industries
Disadvantages:
- Slower welding speeds compared to CW
- Limited penetration depth
- Not ideal for thick materials
Modulated Laser Welding
Advantages:
- Minimal distortion and reduced heat-affected zone
- Suitable for a wide range of materials and thicknesses
- Versatile across various industries
Disadvantages:
- More complex control system
- Requires skilled operators for fine-tuning
- Potentially higher initial setup cost
By considering the advantages and disadvantages of each welding method, you can make an informed decision on the most appropriate technique for your specific applications and requirements.
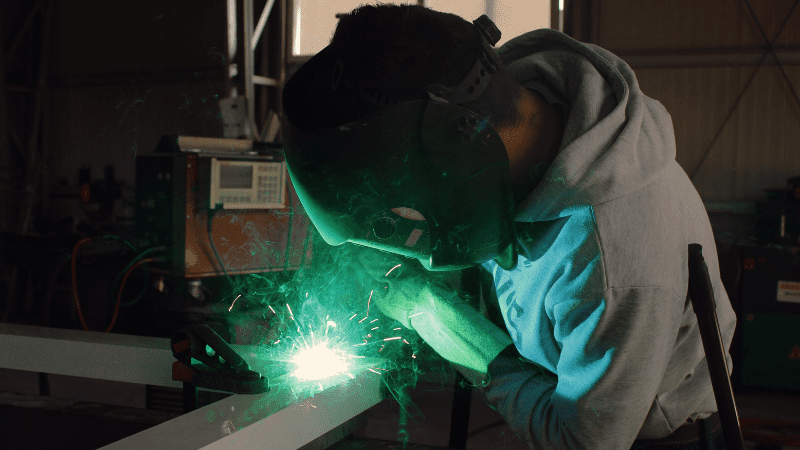
Major Applications of CW, Pulsed, and Modulated Laser Welding
Each laser light welding technique has unique characteristics, making them suitable for specific applications across various industries. Here are the major applications for Continuous Wave, Pulsed Laser, and Modulated Laser Light Welding:
CW Laser Welding
1. Automotive Industry: Welding car body panels, structural components, and exhaust systems.
2. Shipbuilding: Joining steel and aluminum parts in ship hulls, frames, and other large structures.
3. Heavy Industry & Transport: Welding thick materials in construction equipment, railroads, and industrial machinery.
4. Oil and Gas: Fabricating pipes, valves, and other large components that require deep penetration and high welding speeds.
Pulsed Laser Welding
1. Electronics Industry: Assembling printed circuit boards, sensors, and other small, heat-sensitive components.
2. Medical Devices: Manufacturing implants, surgical instruments, and other intricate devices that require precision and minimal heat input.
3. Aerospace: Welding thin materials in aircraft components, such as turbine blades, engine parts, and avionics.
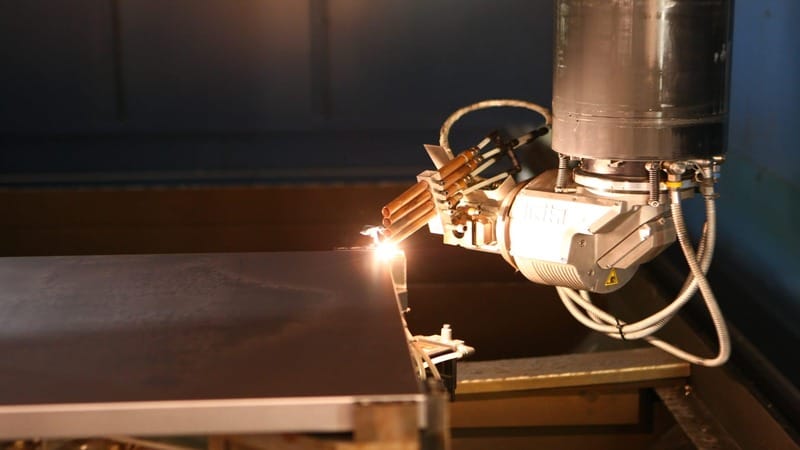
Modulated Laser Welding
1. Appliance Manufacturing: Joining stainless steel parts in household appliances like washing machines, refrigerators, and ovens.
2. Rapid Manufacturing: Producing complex, high-precision parts for industries like aerospace and electronics.
3. Heavy Industry & Transport: Adapting to various material thicknesses and joint configurations in equipment, railroads, and industrial machinery.
4. Custom Manufacturing: Catering to diverse industries and applications that require flexible, adjustable welding parameters.
Conclusion
In conclusion, understanding the differences between CW, Pulsed, and Modulated Laser Welding is crucial for selecting the right lap welding method for your specific needs. Each technique offers unique advantages and is tailored to cater to various industries and applications.
CW Laser Welding excels in deep penetration and high-speed welding. Pulsed Laser Welding is ideal for thin and heat-sensitive materials, while Modulated Laser Welding offers versatility and adaptability across a wide range of materials and thicknesses.
Unlock Your Business Potential with Baison Laser
Take the first step towards achieving excellence in your manufacturing processes by choosing Baison Laser as your trusted partner. With our state-of-the-art laser cutting and welding machines, we’re dedicated to providing you with the perfect solution tailored to your unique business needs. Make a sample proofing request free of cost.