This article will delve into the key to precision laser cutting by examining the most prevalent pipe shapes, discussing their unique characteristics, and exploring their significance in facilitating accurate, high-quality cuts.
What Is Laser Cutting?
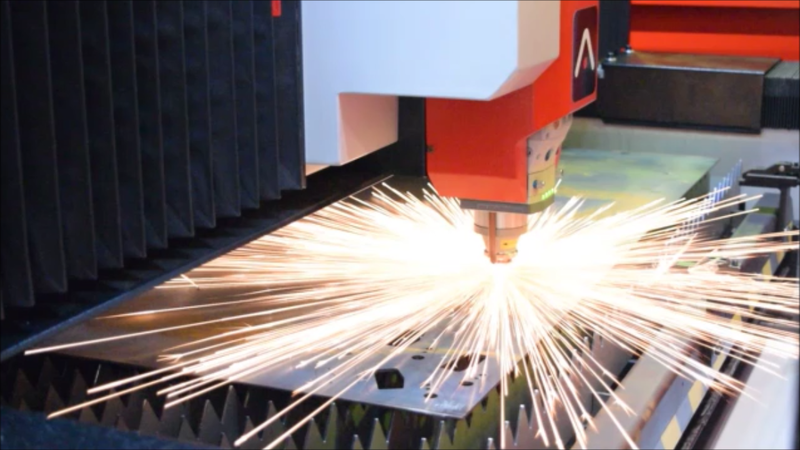
Laser cutting is when a high-intensity laser beam cuts or engraves through materials of various characteristics and thicknesses. It does so with such accuracy and precision that no other method comes close.
Moreover, a wide range of industries, including automotive, aerospace, and electronics, use laser cutting for its ability to produce intricate shapes with minimal material waste.
The fiber laser head sits at heart if we go through the laser cutters’ component breakdown. It houses the laser source and the focusing optics. Additionally, a laser source generates coherent laser beam moves, which the optics focus on the material’s cutting surface. This concentrated energy melts, burns, or vaporizes the material, creating the desired cut or engraving.
A control system directs the laser head to aid and speed up the laser cutting processes. These systems include computer numerical control (CNC) software and hardware that direct the movement of the laser head and the material being processed.
What Are the Common Pipes Shapes and Challenges in Laser Cutting Them?
The laser-cutting metals industry uses a variety of pipe shapes for their unique features and benefits. The most common of these include round, square, rectangular, oval, and angled pipes, among others.
However, each shape presents specific challenges when it comes to fiber laser cutting metal, such as distortion, unevenness, or kerf width variations. Overcoming these challenges is paramount for industries like automotive and construction, where extreme precision is crucial. Let’s learn about each pipe shape separately:
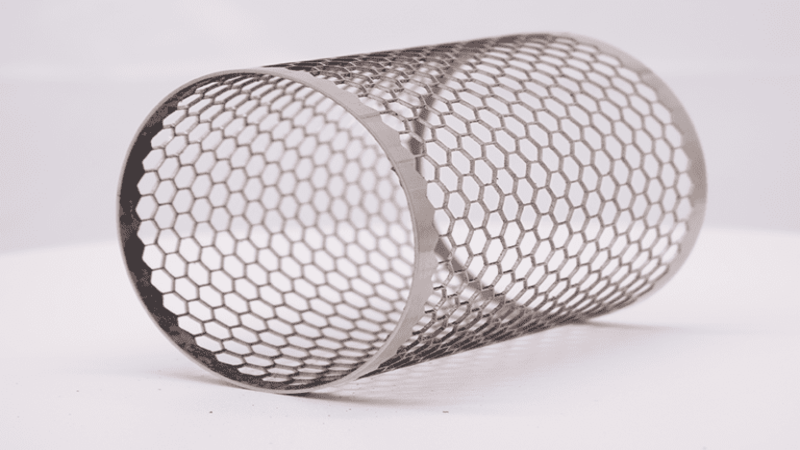
Round Pipes
Round pipes in the laser cutting industry have incredible versatility. Hence, use them for easily adapting to various applications, ranging from structural support to fluid transportation.
Moreover, round pipes offer inherent strength due to their symmetrical cross-sectional shape, which provides an even distribution of force and bending resistance. As a result, this makes them a preferred choice in industries that require durable and robust components.
Common Round Pipe Applications Include:
- Furniture and appliances: round pipes have an aesthetic appeal, making them suitable for table legs or handrails. Moreover, they also have unique functional properties alongside the aesthetic.
- Structural support: In construction and infrastructure projects, round pipes provide strength and stability as scaffolding, columns, or railings components.
- Automotive: Round pipes are used in vehicle frames, roll cages, and exhaust systems. It is their strength and resistance to bending that help with these vehicle components.
Fluid transportation: Round pipes are widely employed in the conveyance of liquids and gases, such as water, oil, and natural gas. All the credit goes to their leak-proof design and smooth internal surface that minimizes friction.
Oval Pipes
Oval pipes feature an elongated, rounded cross-sectional shape. Their unique geometry provides a blend of the benefits of both round and rectangular pipes, offering enhanced aerodynamics and structural integrity.
All this while, the pipes also efficiently maintain a streamlined appearance.
Common Oval Pipes Applications Include:
- Sports equipment: Oval pipes have incredible aerodynamics. This makes them suitable for bicycle frames and other sports gear.
- Automotive: This industry requires exhaust systems that can minimize drag and enhance vehicle performance. Oval pipes are a solid choice for their aerodynamic properties.
- Furniture and appliances: Designers often employ oval pipes to create modern, visually appealing products, such as handrails, shelving units, and lighting fixtures.
- Aerospace: The streamlined shape of oval pipes contributes to reduced air resistance and improved fuel efficiency in aircraft components.
H Steel
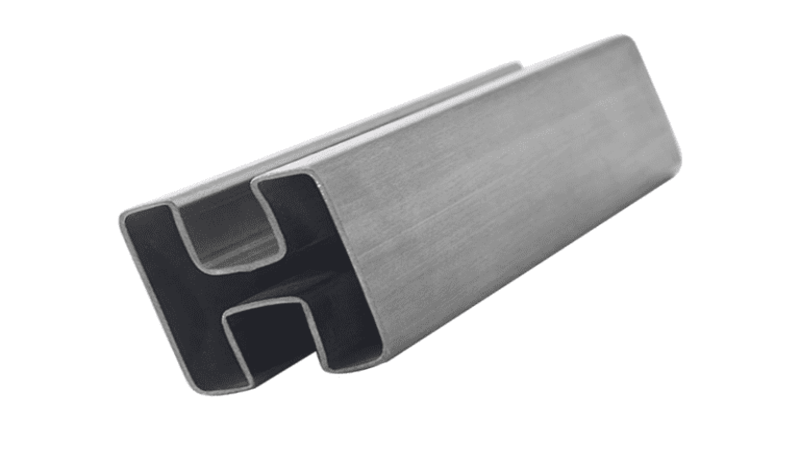
As the name suggests, these pipes have an H-like or I-like cross-sectional shape.
As a result, they have high strength and bend resistance due to the nature of the shape. This makes them ideal for applications where robust support is a must.
Common H Steel Applications Include:
- Construction: This industry readily uses H steel in building frameworks, columns, and beams. All of these have one common functionality, i.e., providing stability and support.
- Industrial equipment: Heavy machinery and production lines may incorporate H steel as structural elements to withstand high stresses.
- Infrastructure: H steel also has incredible loading capabilities, which comes in handy for bridges, tunnels, and other large-scale projects
Square and Rectangular Pipes
Square and rectangular pipes offer excellent rigidity and torsional resistance, making them well-suited for applications with a high demand for stability and structural integrity.
On top of it, they have flat surfaces and sharp edges, which contribute to a clean, modern appearance while also allowing for easier connection and sheet metal fabrication.
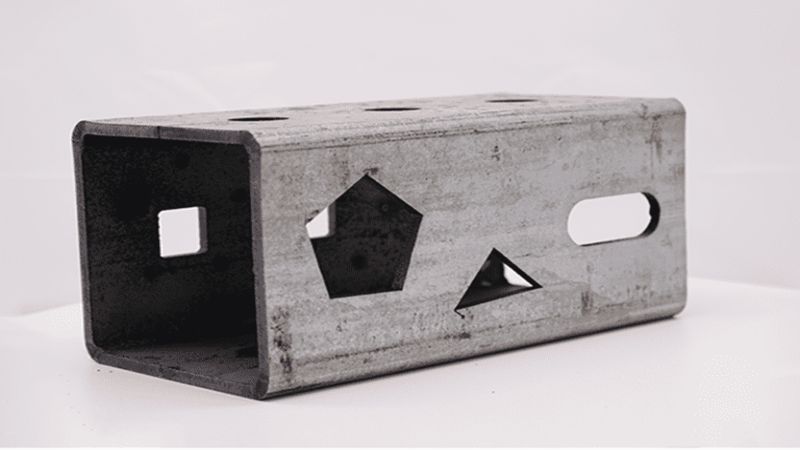
Common Square And Rectangular Pipes Applications Include:
- Construction: pipes greatly help with structural components for bridges, frameworks, and buildings. Moreover, they provide stability and support due to their high rigidity and resistance to twisting.
- Furniture and appliances: Square and rectangular pipes are commonly used to fabricate modern, minimalist furniture designs and appliances. Additionally, their sharp edges and sleek appearance complement contemporary aesthetics.
- Automotive: These shapes are employed in manufacturing vehicle components like chassis, subframes, and supports. Hence, their stiffness and torsional resistance contribute to enhanced performance and safety.
- Mechanical systems: Square and rectangular pipes serve as essential elements in machinery, conveyors, and robotics, where their precise dimensions and consistent cross-sectional properties are crucial.
Angled Pipes
Angled pipes offer the ability to create complex geometries and intricate designs. These pipes’ primary applications require precision, versatility, and customization.
Common Angled Pipes Applications Include:
- Mechanical systems: In machinery and automation, angled pipes play a vital role in creating flexible, multi-directional systems, such as robotic arms and conveyor systems.
- Art and architecture: Angled pipes are widely used in sculptures and modern architectural designs, where their unique geometry contributes to innovative aesthetics.
- Construction: Angled pipes are often used in roof trusses, support beams, and other structural components, where their precise angles provide strength and stability.
- Automotive and aerospace: Complex structures in vehicles and aircraft often employ angled pipes to optimize weight distribution and increase overall performance.
U-shaped Steel
U-shaped steel, also known as U-channels or C-channels, features a U-shaped cross-sectional profile with parallel flanges.
These shapes offer excellent strength and stability while being relatively lightweight, making them well-suited for various applications.
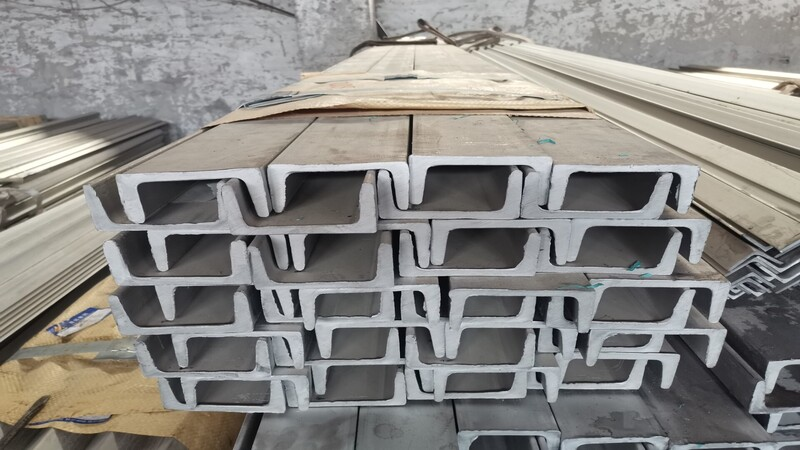
Common U-Shaped Steel Pipes Applications Include:
- Industrial equipment: Conveyor systems, storage racks, and other industrial structures often incorporate U-shaped steel for their durability and load-bearing capabilities.
- Construction: U-shaped steel is often used in building frames, roofing, and floor support systems, where their load-bearing properties are essential.
- Automotive: Vehicle frames and structural components can utilize U-shaped steel for added strength and stability.
Angle Iron
As the name suggests, this pipe has an angled or L-shaped shape. It consists of two perpendicular flanges forming a 90-degree angle.
This shape provides excellent strength and stability, making it suitable for a wide range of applications.
Common Angle, Iron Pipes Applications, Include:
- Construction: Angle iron is widely used as structural components in buildings, bridges, and support frameworks, where their rigidity and resistance to bending are crucial.
- Automotive and machinery: Angle iron can be found in various vehicle components and machinery, where its strength and stability contribute
- Shelving and storage: The 90-degree angle profile of the angle iron makes it ideal for creating sturdy shelving units and storage racks.
Techniques for Laser Cutting Common Pipe Shapes
Here are some vital techniques to utilize when working on a laser cutting pipes project:
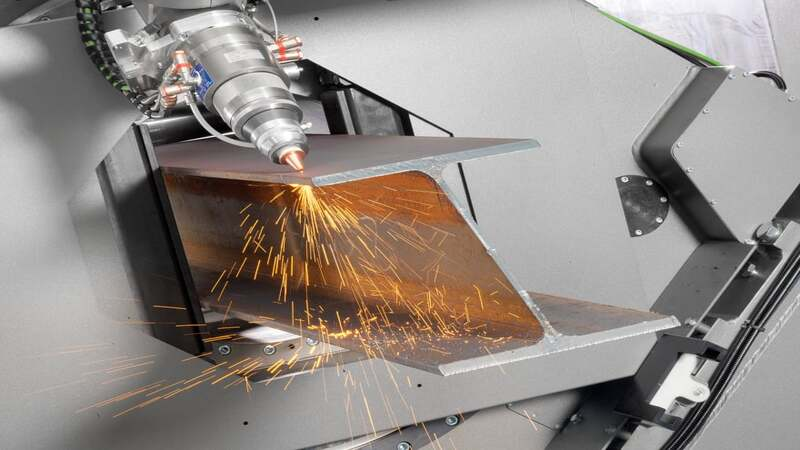
1. Rotary Axis Cutting: This method involves the use of a rotary axis, which rotates the pipe during the cutting process. This ensures that the laser beam remains perpendicular to the surface of the pipe, resulting in consistent kerf width, reduced distortion, and improved accuracy.
2. Adaptive Cutting: In some cases, adaptive cutting techniques can be used to modify the cutting speed and laser power in real time based on the pipe’s geometry and material properties. This allows for better control over the cutting process and ensures consistent results across different pipe shapes.
3. Automatic Focus Control: Maintaining the correct focus distance between the laser head and the pipe surface is crucial for achieving optimal cutting results. Automatic focus control systems adjust the height of the laser head in real-time to maintain the ideal focus distance, ensuring consistent cut quality across the pipe’s surface.
4. Programmable Assist Gas: The use of assist gases, such as nitrogen or oxygen, can help reduce heat-generated zones, minimize oxidation, and improve cut quality. Programmable assist gas systems allow operators to adjust gas pressure and flow rates according to the specific material and cutting requirements, optimizing the cutting process.
5. 3D Laser Cutting: Advanced laser cutting machines equipped with 3D cutting capabilities allow for more precise and intricate cuts on complex pipe shapes. 3D laser cutting provides greater flexibility in cutting angles, allowing for creating custom geometries and profiles.
6. Advanced Nesting Software: To optimize material usage and minimize waste, advanced nesting software can be employed to arrange parts efficiently on the pipe. This software considers the pipe’s shape and dimensions and the desired cut patterns to maximize material utilization and reduce production costs.
Factors That Affect the Choice of Pipe Shapes in Laser Cutting
The choice of pipe shapes for laser cutting is influenced by several factors that determine the suitability and efficiency of a particular shape for a specific application. These factors include:
1. Thickness: The thickness of the pipe material affects the choice of pipe shape, as certain shapes may be more challenging to cut with consistent quality at varying thicknesses. Thicker materials may require slower cutting speeds, higher laser power, or specific assist gases to achieve optimal results.
2. Application: The intended use of the final product plays a significant role in determining the most suitable pipe shape. Different applications require different properties, such as strength, rigidity, torsional resistance, or aesthetics, which specific pipe shapes can provide.
3. Size: The size and dimensions of the pipe being cut are crucial factors in determining the appropriate shape. Depending on the application’s requirements and the laser-cutting machine’s capabilities, some pipe shapes may be more suitable for larger or smaller dimensions.
4. Material: The material being cut also influences the choice of pipe shape, as certain materials may be more compatible with specific shapes due to their mechanical properties, such as elasticity, hardness, or thermal conductivity. The material also impacts the cutting speed, quality, and the choice of laser source and assist gas.
To make a perfect effect, you need to learn what materials a fiber laser can cut.
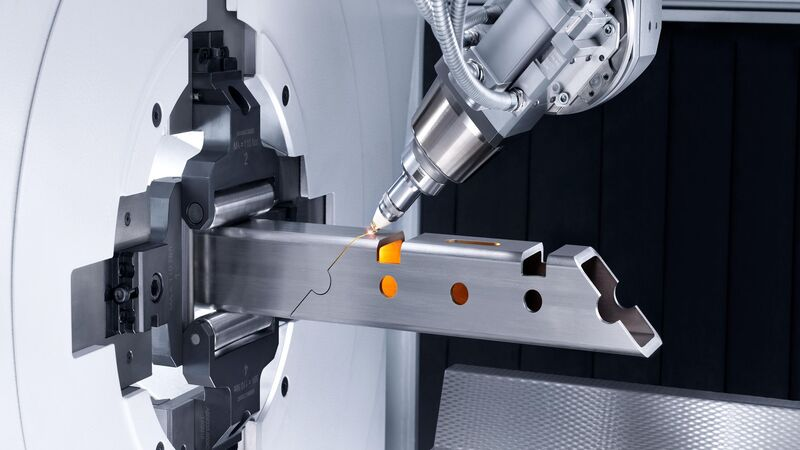
Here are some vital factors to consider to find the most suitable pipe type for your application. For instance:
- Round pipes are ideal for fluid transportation and structural applications requiring resistance to bending and even force distribution.
- Angled pipes, H steel, U-shaped steel, and angle iron are well-suited for complex construction, automotive, and machinery structures, where intricate cutting patterns and extreme precision are required.
- Oval pipes provide a combination of aerodynamic and structural benefits, making them suitable for automotive and aerospace applications where reduced air resistance and fuel efficiency are important.
- Square and rectangular pipes offer excellent rigidity and torsional resistance, making them suitable for construction and mechanical systems where stability and structural integrity are critical.
What Are the Special Shapes and Custom Designs?
Special shapes and custom designs refer to unique pipe geometries created using laser-cutting technology to meet specific requirements or applications. These shapes deviate from standard pipe forms like round, square, or rectangular, offering tailored solutions for businesses with particular needs.
Laser cutting technology provides the flexibility and precision necessary to produce a wide range of custom pipe shapes, such as:
1. Multi-faceted pipes: Pipes with multiple flat surfaces or complex geometries used in intricate structural designs or machinery.
2. Curved pipes: businesses use curved pipes mainly for their non-linear aesthetic profile. Moreover, it offers unique functionalities that are essential, such as decorative elements or custom automotive components.
3. Tapered pipes: Pipes with varying diameters along their length, utilized in applications requiring graduated fluid flow or specific weight distribution.
The Benefits Of Custom Designs For Businesses Include the following:
1. Enhanced functionality: you can also benefit from custom pipe shapes to meet specific performance requirements. This helps provide optimized solutions for particular applications.
2. Material and cost savings: you can optimize custom designs to reduce material waste and lower production costs. Hence, this results in a more efficient manufacturing process.
3. Competitive advantages of laser cutting: Unique pipe designs can help businesses differentiate their products from competitors, showcasing innovation and expertise.
Applications and Designs of Laser Pipe Cutting
Here are the applications and designs of laser pipe cutting:
Applications:
1. Aerospace: Aircraft frames, structural supports, and engine parts.
2. Construction: Structural components, such as beams, columns, and trusses.
3. Furniture and appliances: Modern, minimalist designs and functional components.
4. Industrial machinery: Conveyor systems, robotic arms, and assembly lines.
5. Automotive: Vehicle frames, exhaust systems, and chassis components.
Designs:
1. Hole cutting: Precise cutting of round, square, or custom-shaped pipe holes for connections or ventilation purposes.
2. Angle cutting: Creating precise angles and miters for better fitting and assembly of structural components. Learn about how to cut angled pipes with a pipe-cutting machine.
3. Pattern cutting: Intricate and repetitive patterns for decorative elements, fencing, or unique components.
4. Arc cutting: Curved cuts for aesthetic or functional purposes, such as pipe bending or forming complex geometries.
5. Letter cutting: Cutting letters or symbols into pipes for branding, signage, or decorative purposes.
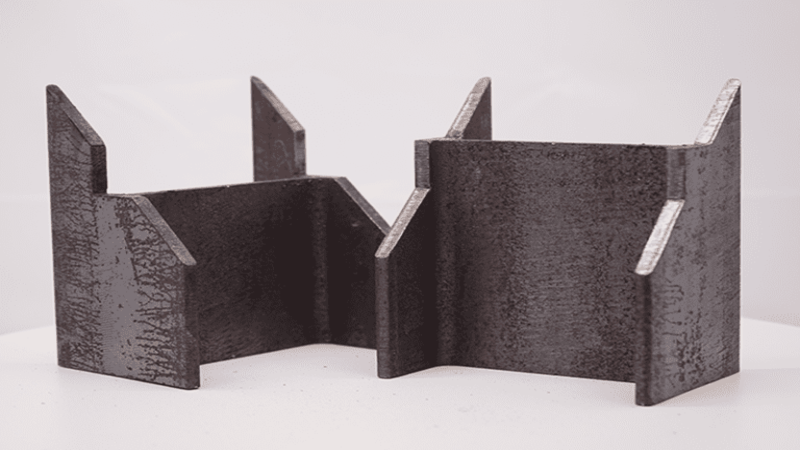
How to Choose a Laser Cutting Service Provider?
Selecting a reliable and experienced laser-cutting service provider is crucial for ensuring the quality and efficiency of the final product. Several factors should be considered when choosing a provider, including:
1. Customization capabilities: Determine if the provider can accommodate custom designs or special shapes according to your project requirements. A versatile laser-cutting service should offer tailored solutions for unique applications.
2. Experience and expertise: Evaluate the provider’s years of experience and technical expertise in the industry. A well-established company with a proven track record is more likely to deliver high-quality results.
3. Equipment and technology: Look for a provider with advanced laser cutting machines featuring the latest technology and capabilities. This ensures that the company can handle a wide range of materials, thicknesses, and shapes with precision and speed.
4. Customer support: Evaluate the company’s responsiveness and level of customer support, ensuring that they provide clear communication and address any concerns promptly.
5. Quality assurance: Investigate the company’s quality control processes and certifications, such as ISO or ASME, which demonstrate their commitment to maintaining high standards and delivering consistent, precise cuts.
6. Turnaround time: Assess the provider’s ability to meet your project deadlines and offer a reasonable turnaround time. A reliable service provider should have the capacity to handle your project efficiently and within the stipulated timeframe.
Conclusion
In conclusion, understanding common pipe shapes and their unique characteristics is essential for achieving precision in laser cutting applications. By considering factors that influence the choice of pipe shapes and utilizing advanced cutting techniques, businesses can optimize their production processes and create custom designs to meet specific requirements.
Also, explore other resources on our website further to enhance your knowledge of laser cutting and welding machinery and discover how our products and services can help elevate business operations.
Experience Unparalleled Laser Cutting Solutions With Baison
Baison is committed to providing businesses with cutting-edge laser cutting and welding solutions tailored to their unique needs. Our state-of-the-art equipment and experienced team of professionals ensure precise and efficient results, enabling you to streamline your production processes and gain a competitive edge.
Let us help you unlock your business’s full potential with our innovative laser technology solutions. Get in touch today!