In recent years, laser cutting technology has captured the manufacturing industry due to its high efficacy, precision, and throughput. Manufacturers are now utilizing laser technology to cut and shape most types of metals, including mild steel, aluminum alloy, stainless and galvanized steel, etc.
Among other materials that can be cut with a laser, carbon steel plates and tubes stand out due to their widespread use in manufacturing and construction.
We have prepared this definitive guide to provide you with the details of laser-cutting carbon steel plates. We will cover everything from the basics of laser cutting technology to the factors affecting edge quality.
So, whether you’re new to the world of laser cutting or looking to refine your skills, this guide will be a valuable resource for mastering the art of cutting carbon steel.
What Is laser cutting?
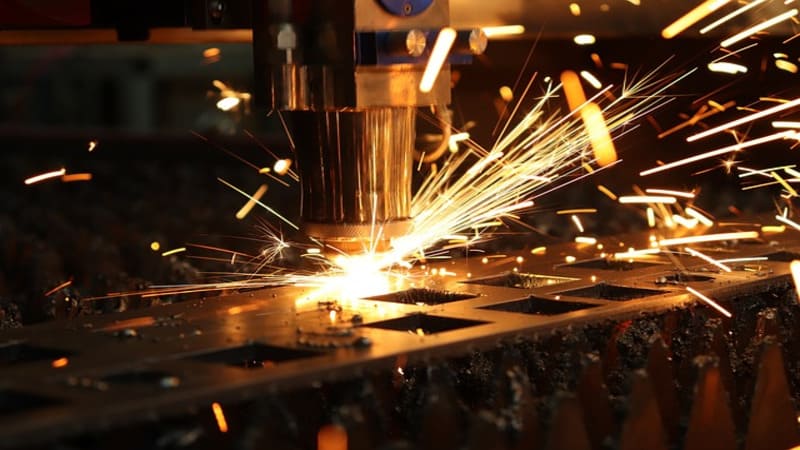
As the name suggests, laser cutting is a manufacturing process in which sheet metal is cut via laser. In this process, the metallic workpiece is placed in a laser cutting machine, in which a high-intensity laser beam melts, vaporizes, and cuts the materials.
Compared to conventional cutting processes, the laser cutting process is highly accurate and precisely cuts out all types of metals, including aluminum alloys and mild and carbon steel sheets. That is why laser technology is significantly gaining popularity.
The laser cutter system can have fiber or CO2 technology based on the medium used to generate and propagate the fiber laser. Fiber lasers are more prevalent in the laser-cutting sector.
What Are the Characteristics of Carbon Steel?
Carbon steel is an iron alloy containing carbon as the main alloying element. The carbon content ranges from 0 .05% to 2.0%, where the higher percentage indicates more hardness and strength.
Some of the key properties of carbon steel include its high tensile strength, good machinability, and ability to be heat treated for increased hardness. It is also relatively easy to weld and form into different shapes, making it a versatile material in manufacturing.
Types of Carbon Steel Commonly Used in Industrial Applications
Based on the percentage of carbon content, there are several types of carbon steel. Some of the common ones used by manufacturers include:
- Low-Carbon steel contains up to 0.30% carbon and is used for applications that require good formability and weldability. Being ductile, this type of steel is used for making pipes and valves.
- Medium carbon steel contains 0.30% to 0.60% carbon and is used when higher strength and wear resistance are required. Its common applications are mechanical parts such as crankshafts and railway tracks.
- High carbon steel contains 0.60% to 2.0% carbon and is used for applications that require high strength and hardness, such as cutting tools and springs.
Carbon Steel Type | Carbon Content | Industrial Grades | Applications |
Low Carbon Steel | 0.05% – 0.30% | A36, ASTM 1010, 1020 | Building construction, welding, machining |
Medium Carbon Steel | 0.30% – 0.60% | ASTM A229, 2029 | Gears, shafts, axles, machinery parts |
High Carbon Steel | 0.60% – 2.00% | 1095, A440 | Knives, blades, cutting tools, springs, machinery |
How Carbon Content Affects the Properties of Steel?

Since carbon is the main content in this iron alloy, all the mechanical properties ultimately depend on it. The above stress-strain visual depicts this behavior.
As the carbon content increases, the steel becomes harder and stronger, but its brittleness also rises. Furthermore, the high-carbon content reduces the weldability and ductility of the steel, making it more challenging to work with.
Conversely, lower carbon content increases the steel’s formability but reduces its hardness and strength. However, when the carbon content is in the median range, the material is most challenging, i.e., it has high strength as well as ductility.
How does Laser Cutting Work on Carbon Steel?
The laser cutting on carbon steel works on a similar principle we mentioned earlier in the laser cutting section. The laser beam strikes the surface of the carbon steel and heats the material to the point where it melts and vaporizes, creating a narrow, clean cut.
The cutting process is controlled with high precision using CAD software, allowing intricate and complex shapes to be easily cut. The type and power of the laser cutting machine will depend on the metal sheet thickness being cut.
Factors That Can Affect the Quality of Laser-cutting Carbon Steel Plates and Tubes
The quality of laser cuts is affected by multiple factors. Some of the key factors that need to be controlled include the following:
Material Thickness and Pipe Diameter:
The thickness of a metal sheet and pipe diameter are primary factors that affect the quality of the cut. Thicker materials require more laser power and slower feed rates, while thinner materials require less power and faster feed rates.
Also, the fiber laser cutting machines do have thickness constraints. Most of them can cut up to a wall thickness of 2.75 inches. The same is the case with pipe diameter. Our fiber laser tube cutting machine can cut a pipe diameter of 19.69 inches.
Laser Power:
The laser power determines the beam’s intensity and can affect the quality of the cut. Higher laser power can work with faster cutting speeds and provide better edge quality. However, it may not be suitable if sheet metal is beyond a certain thickness.
Feed Rate:
The feed rate is the laser’s speed across the material. It can affect the quality of the cut by controlling the amount of heat that is generated. Higher feed rates can result in faster cutting speeds, but they may also reduce the quality of the cut.
Focus:
The focus of the laser beam can affect the quality of the cut. A properly focused beam will produce a clean, precise, and consistent cut, while an unfocused beam can result in a wider kerf and lower edge quality.
Gas selection:
Oxygen, nitrogen, and compressed air are commonly used as assist gases for laser cutting carbon steel. However, the appropriate gas is selected based on the material thickness and type of carbon steel. Generally, oxygen is used in the laser cutting of mild steel.
Air Pressure:
The air pressure used to deliver the assist gas also affects the laser cut. Too much pressure can cause material deformation or oxidation, while too little pressure can result in incomplete cuts or poor edge quality.
What Are the Advantages of Laser Cutting Carbon Steel?
Laser cutting is an advanced process and it does offer multiple advantages over traditional cutting methods. Some of the key ones are:
- Laser cutting results in precise cuts with tight tolerances, allowing for complex shapes and designs.
- It is a fast-cutting method that can cut through thick materials quickly and efficiently.
- Through a fiber laser cutting machine, we can cut through a wide range of materials, including carbon steel, stainless steel, aluminum, and plastics.
- The focused laser cutting produces clean, smooth edges that require minimal finishing. Thus, reducing the need for additional processing.
- Since the laser is sharply directed to a target area, a minute quantity of waste is produced during the cutting process. This further reduces material costs and improves efficiency.
- Laser cutting can be fully automated, reducing labor costs and improving productivity.
- Despite the initial investment in equipment, fiber laser cutting can be cost-effective in the long run due to its precision, speed, and reduced waste
- Laser cutters don’t give off any significant fumes or emissions, making it a more environmentally friendly cutting method compared to traditional cutting methods.
- Laser-cutting machines produce minimal noise and vibration, reducing the risk of worker injury and fatigue.
Common Problems During the Laser cutting process
Laser cutting doesn’t always produce perfect results like other manufacturing processes. Some problems may sometimes occur, resulting in defects within the sheet metal.
Here’s a list of some common problems that you can face during the laser-cutting process:
Wide Incision at the Bottom

In some cases, you will observe that the produced incision is wider and the traction line offset (refer to the above figure). In this circumstance, either the laser power and air pressure are set too low or the feed rate and focus are set too high. Reset these parameters to fix the problem.
Dripping Burr from the Bottom Surface
When the feed rate and focus are set high, the surface of the steel plate will burr on the surface, like a slug. You will notice that it drips along the bottom surface. You can consider raising the focus and feed rate to fix the issue.
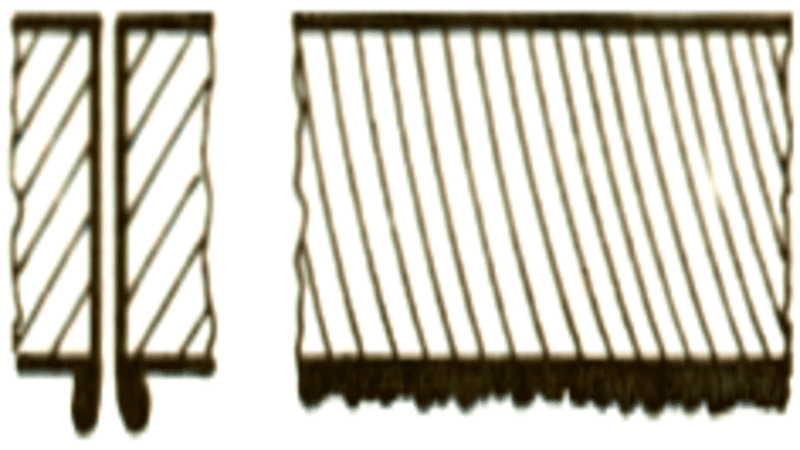
Only the Upper Section of Sheet Metal Is Removed
When the parameters aren’t selected according to the sheet metal thickness, the cutting action isn’t performed successfully, resulting in an incomplete cutting operation. In that case, you need to lower the feed rate and raise the laser power.
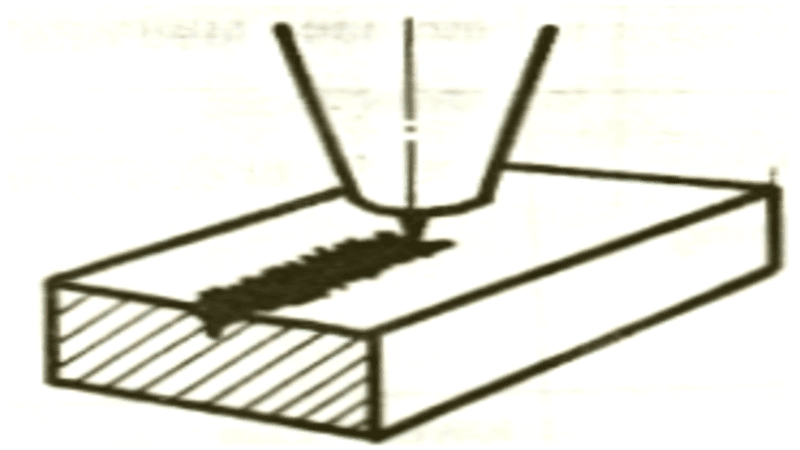
Cutting Yields a Rough Surface
In some cases, the surface produced lacks precision. It can be due to multiple reasons including a damaged nozzle, high air pressure, or poor surface finished metal plate. To fix the problem, you can try decreasing the air pressure, replacing the nozzle, or cleaning the metal surface.

How to Prepare Carbon Steel Plates and Tubes for Laser Cutting?
Here’s a step-wise guide to preparing carbon steel plates and copper tubes for laser cutting:
Step 1: Clean the Material
Place your metal sheet on a safe spot and remove any dirt, oil, or other contaminants from the surface. To do so, you can use a solvent or a degreaser.
Step 2: Remove Surface Coatings
If the metal plate bears any surface coatings, for instance, paint or rust, get rid of them before the laser cutting operation. You can remove these coatings via a chemical stripper or mechanical methods such as grinding or sandblasting.
Step 3: Flatten the Material
The metal sheet must be flat for the laser to hit precisely. So, it would help if you made sure the material was flat and free from any warping or distortion. You can achieve that with a roller. This step doesn’t apply to a metal tube, but you must ensure it is flat.
Step 4: Secure the Material:
Once the metal plate or tube is cleaned and factory ready, secure it to the cutting bed to restrict its movement cutting. You can use clamps or magnets, whatever is placed in that machine.
Applications of Laser Cutting carbon steel
Laser cutting is used for cutting carbon steel, which has extensive use in a wide range of industries from aerospace and automotive to the construction and advertisement industry. You can refer to table 2 to see the applications of laser cutting in a range of industries.
Industry | Applications |
Aerospace | Sheet metal, tubing, and composite components |
Automotive | Exhaust systems, body panels, frames |
Construction | Steel plates, tubes, and beams for buildings, bridges, tunnels |
Energy | Heat exchangers, turbines, pipelines |
Medical Devices | Surgical instruments, implants, diagnostic equipment |
Signage | Metal cutting and engraving for signs and displays |
Oil and Gas | Components for oil rigs, pipelines, and storage tanks |
Agriculture | Components for farming equipment and machinery |
Metal Processing | Cutting, drilling, welding, and shaping metal for various industrial uses |
Shipbuilding | Components for ships and boats |
Quality Laser Cutters to Cut Carbon Steel
The quality of a laser cutting machine can play a critical role in achieving desired results when cutting carbon steel plates and tubes.
We at Baison laser develop high-quality laser cutting machines that can precisely sheet metal tubes. Even, our entry-level sheet metal laser- cutting machine has a position accuracy of ±0.05mm/m.
Similarly, we have laser tube cutting machines, that are capable of cutting pipes of any length and large diameters with great accuracy.
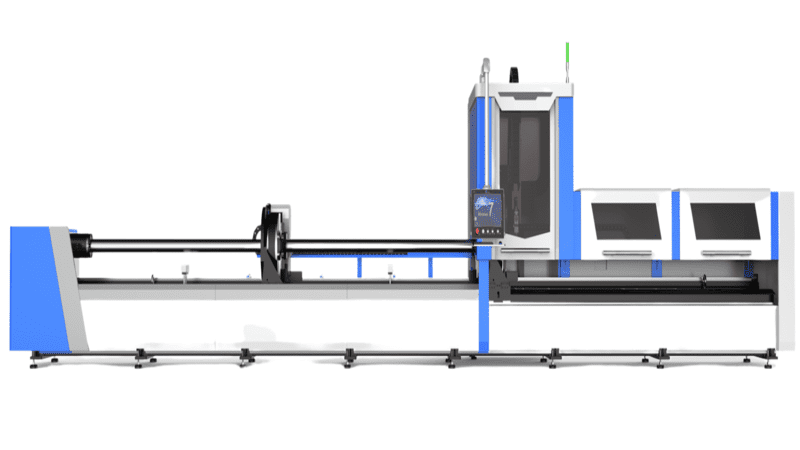
How to Get Perfect Cuts with the Help of a Laser Cutter?
To get the most out of laser cutting, it is essential that you can adhere to the following instructions:
Prepare the Material
The laser beam strikes the sheet metal to cut. So, if the workpiece itself has a poor surface, the laser won’t cut efficiently, resulting in a rough cutting surface. So, it is necessary to prepare the material before cutting it.
Choose the Right Assist Gas:
The choice of assist gas can affect the cut’s quality and the process’s speed. Oxygen is often used for thicker materials, while nitrogen is used for thinner materials.
Optimize the Cut Path:
Use software to optimize the cut path, considering the material’s shape and thickness. This can help minimize the number of cuts and reduce waste.
Ensure Proper Machine Settings:
After all preparation steps and cleaning is done, set the laser power, speed, and focus correctly for the material being cut. This can be done using the machine or system’s control panel or software.
Conclusion
Laser cutting is a highly effective method for cutting carbon steel plates and pipes. Though the method seems complex, we believe that this guide would have helped you understand the basics of laser cutting. When optimizing the laser-cutting process, it is essential to consider factors such as material thickness, laser power, feed rate, focus, and air pressure.
Baison laser is one of the pioneer manufacturers of laser cutting machines. We have developed a range of fiber laser cutting machines to cut through any sheet or pipe.
If you’re looking for a comprehensive solution to your cutting needs, then your can test our products. Contact us now to get a quote or customized help from our experts.