Identifying which is best suited for your marking, cutting, and engraving projects requires in-depth knowledge.
In this article, we’ll discuss laser cutting and optimizing the machine. We’ll explain the features, types, and materials used to make crossbeams. You’ll also learn the tips for choosing the right equipment and benefits. So, let’s dig into the details.
What Is Laser Cutting
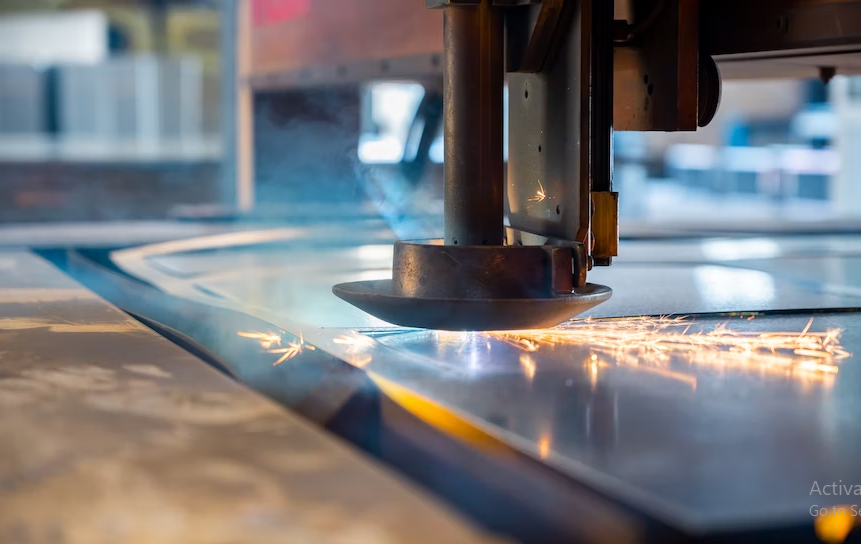
Laser cutting is a thermal process where a high-powered machine produces intense, concentrated heat to etch or vaporize materials. It involves directing the device beam, also called light, through laser optics on metallic and non-metallic items for an edge-quality finish.
As the focused laser beam becomes hotter and thinner, the cutting head melts through acrylic, plastic, living hinges, and even sheet metal.
The laser cutting process ideally allows you to recreate excellent designs quickly. You might produce specified patterns with precise cuts using this computer-controlled machine with accurate motion systems.
Importance of Optimizing Laser Cutting Machines
Optimizing the machine means making it more efficient and effective for industrial cutting. The process helps laser-cutting technology achieve new accuracy and performance.
The importance of enhancing your laser cutting equipment is as follows:
- Transforms the machine performance to deliver high precision with accuracy
- High acceleration with dramatic improvement in rigidity
- Flexibility to cut thick and thin materials into different sizes
- It improves dynamic positioning and minimizes clogging.
What Are Crossbeams?
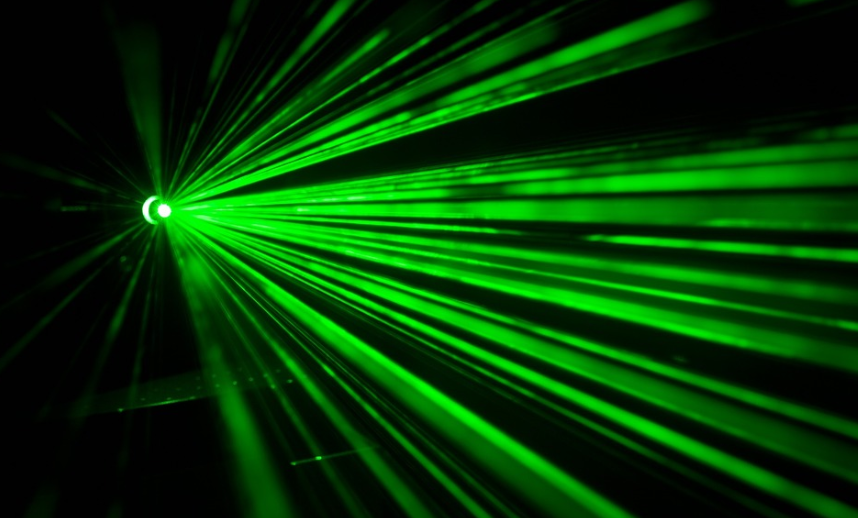
Crossbeams are groups of light rays from a source with stable frequency. These beam waves produced by a laser cutting machine have similar wavelengths. They travel together with their peaks in line and could bounce in different directions.
These light waves are bright, narrow, and easy to focus on in a specific direction. They’re often used for surface modification and to cut, mark, engrave, and drill various materials. You can trim, shape and etch objects with a focused laser beam.
Features of Crossbeams
Brightness, directionality, and coherence are essential crossbeam characteristics. Monochromacity and collimation are other features to know.
Monochromatic: The laser emits photons with the same energy, leading to an identical color (wavelength).
Coherence: The light waves are in line or phase temporally and structurally.
Collimation: All light rays don’t diverge significantly and are parallel to each other
Directionality: Emits lights in a specific direction
Brightness: Produce brighter lights compared to other sources.
Types of Crossbeams
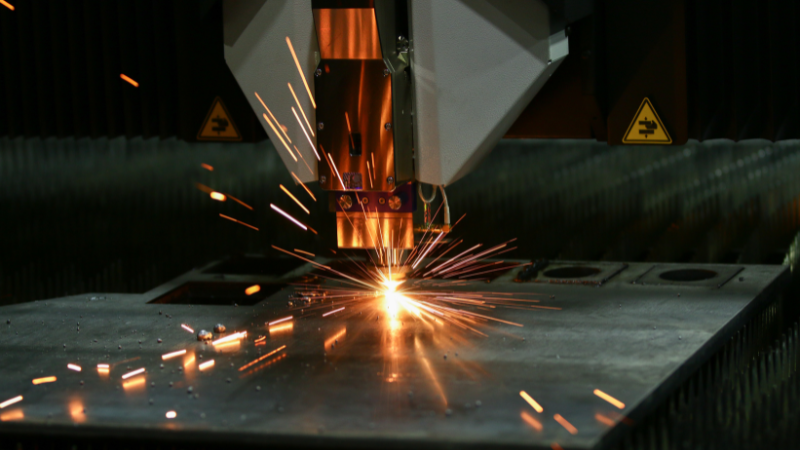
These light rays produced by a laser machine have various types. Some of them include the following:
Parallel: Crossbeams are parallel when the light rays don’t meet at a particular point.
Convergent: The light rays from the stable light source meet at a point with a convergent crossbeam
Divergent: It’s called divergent crossbeam when the lights move away from the source.
What Materials Can Be Used to Make Crossbeam
Gain medium, pump source, and resonator are materials used to make crossbeams for cutting and melting objects. Here are the details:
Gain Medium: These materials determine the laser emission properties. Examples include semiconductors such as aluminum and aluminum gallium arsenide and ions in glasses or crystals.
Consider molecular and atomic gases such as nitrogen and carbon dioxide as a gas laser cutting equipment’s gain medium.
Pump source: Various pumping mechanisms can make laser cutter crossbeam, but the gain medium often dictates it. Energy propellants such as electric current and discharge are a few examples. Arc or flash lamps are other pump sources to consider.
Laser Resonator: The powerhouse of a high-powered laser cutting machine consists of a glass tube containing helium, nitrogen, and hydrogen. Examples of laser resonators include coated or cleaved facets in a laser diode or bulk mirrors in a solid state.
Considerations for Choosing the Right Crossbeam
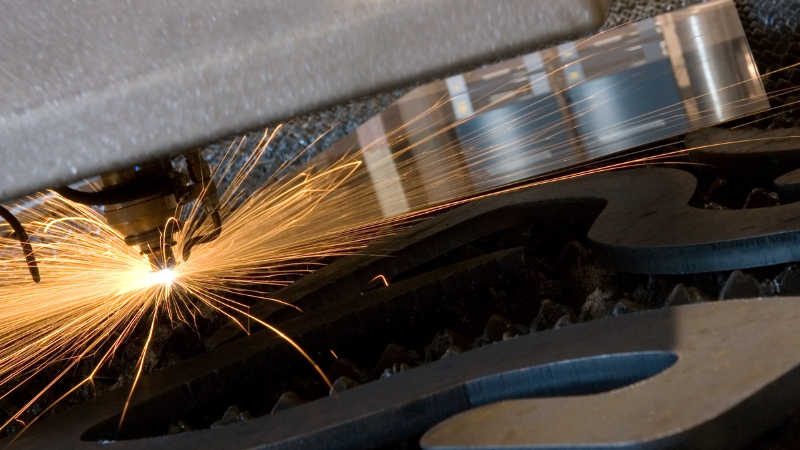
Many beginners make mistakes when selecting the best crossbeam due to the available varieties of laser cutting machines. Consider various factors when choosing suitable light rays to engrave and cut materials.
Power and Wattage of the Laser
The laser power and wattage are essential considerations for the right crossbeam. They determine how much energy the equipment can deliver, influencing light rays’ quality.
A higher-powered machine can easily engrave deeper into surfaces or cut through thicker materials.
A machine with 30 – 100 watts is sufficient for most applications. Since welding larger parts and cutting thick materials requires high-power equipment, CO2 and fiber lasers are ideal. They allow you to use the engraving option with the right settings.
Material Thickness
Crossbeams are best for materials with less than 20 mm thickness. So consider the thickness of the object you’re cutting before purchasing.
When cutting a metal sheet or mild steel, you may need a 20–25 mm fiber laser machine. It might also engrave or drill thicker plastic, leather, glass, and ceramics.
When etching objects above the threshold, the cutting speed might become low, affecting the cut quality. Guiding the light rays through thick materials with a CO2 or fiber laser machine could also challenge beginners.
As the thickness increases, the gas pressure and machine energy reduce, lowering material removal efficiency from the laser head.
Cutting Speed and Accuracy Requirements
Since cutting speed is directly related to the machine power, consider the accuracy requirements when choosing the right crossbeam. The best way to check the laser geometric and positioning cut precision is by testing it on the material and examine with a microscope.
You can achieve a small cut width of fewer than 0.0001 inches with laser machines. With the equipment, getting a dimensional accuracy of approximately ± 0.0005 inch is also possible.
You can now cut and drill metals correctly thanks to computer numerically controlled CNC machines.
Durability and Maintenance
Maintenance and durability are crucial when selecting a crossbeam because they determine longevity. Check the laser housing and ensure it can withstand pressure, harsh conditions, and wear before buying.
The productivity and efficiency of your equipment depending on how easy they are to manage. Consider choosing crossbeams with seamless maintenance for desired results.
Benefits of Choosing the Right Crossbeam
The most suitable crossbeam for your machine makes accomplishing tasks seamless. Here are the benefits:
Higher Cutting Speed and Accuracy
Expect increased cutting speed and accuracy from a laser cutting service with the right crossbeam. The ray of light cuts through materials in a short period. It’s a lot faster than engraving and drilling metals the traditional way.
With ultimate precision, you can etch and cut glass, ceramics, wood, and plastic. Its high accuracy benefits metalworking, HVAC, woodworking, and manufacturing professionals.
Longer Lifespan of the Laser Cutting Machine
Another benefit of choosing the right crossbeam is the longevity of your laser cutters. Proper maintenance also enhances the machine’s lifespan and ensures the device function at an optimum.
Since the equipment has an excellent power rating and cutting speed, it accomplishes tasks with high speed. It reduces your cutting tool’s functioning time, which increases its lifespan.
Reduced Repair Costs
The crossbeam doesn’t touch the material you’re engraving or etching during the laser cutting process. It minimizes the risk of damage to your tool and item’s surface.
You don’t have to buy new materials to complete projects after using the laser system. It prevents delayed completion times and ultimately reduces repair costs.
Cutting wood or other flat objects might create debris, smoke, and fumes. The right crossbeam keeps the money for repair in your pockets because its components might not need replacing.
Enhanced Productivity and Efficiency
Select the appropriate crossbeam to enjoy improved efficiency and productivity. The processes are not time-consuming, yet they produce fast results.
You can quickly perform complex marking, cutting, and engraving with the right laser cutting machine.
Illustrators, photo editing with layout, and graphic design software are effective programs for laser machines. They have solid visual references, such as grids and rulers, that make complex tasks seamless.
How to Maximize Efficiency and Safety With a Crossbeam
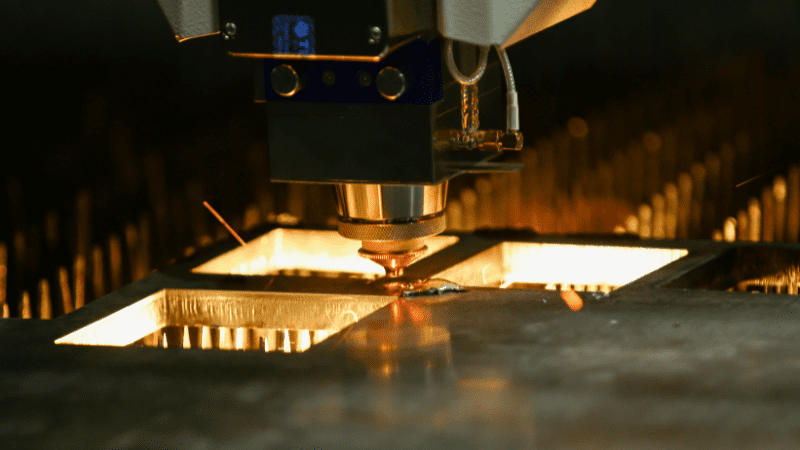
You must realize how crucial it is to maximize efficiency and safety with a laser cutter crossbeam. Failure to do so might lead to poor cutting. Ways to improve your machine include:
Step 1 – Optimize Laser Cutting Parameters
These parameters are the core technologies behind laser cutting systems. The properties include power, wavelength, coherence length, pulse width, and spot size. They determine the crossbeam cut quality and speed, so optimizing them improves working efficiency.
Step 2 – Introduce High-Quality Cutting Head
Using a high-quality cutting head ensures stable engraving and marking quality and improves safety. You also don’t need to replace the tool regularly, which maximizes work efficiency.
Step 3 – Use Design Systems
Maximize efficiency with a crossbeam by integrating software packages that support laser cutters. You can optimize design systems with Autodesk Inventor and create high-quality patterns with Adobe Illustrator.
Step 4 – Regular Maintenance
Another way to improve safety and efficiency with light rays is regularly maintaining the laser cut parts. Check and clean the lens optical part system if they become rusty after working for a while. Replace worn parts and lubricate the machine after a period of operation.
Conclusion
Now you know the importance of optimizing laser cutting machines and choosing the right crossbeam. The best equipment should offer durability and flexibility and precisely cut thick or thin material.
You make key holders, drink coasters, and kitchen appliances with a fiber or CO2 laser cutting machine.
Buy efficient laser cutting systems with productive features only from reputable producers. Baison laser fits the description of the best manufacturer for this equipment. Contact us today for a consultation, and we’ll provide cost-effective and durable products to satisfy your needs.