One of the two is normally better than the other when you look at the project you need to accomplish. Laser and water jet cutting have several pros and cons to help you choose the best method. You need to look at the material you need to process, the turnaround time for the project, and even the cost of the whole process.
Let’s cut through the difference between the two and determine what is good and bad for each process. This will help you determine which cutting technique you need to use.
What is laser cutting?
Laser cutting is one of the techniques preferred by many people in the industry, but there are a few things you need to keep in mind. As popular as it is, there are some factors you need to look at before choosing laser cutting. You need to consider materials and applications and the technique’s safety. Not to mention the cost involved in setting up a laser-cutting process.
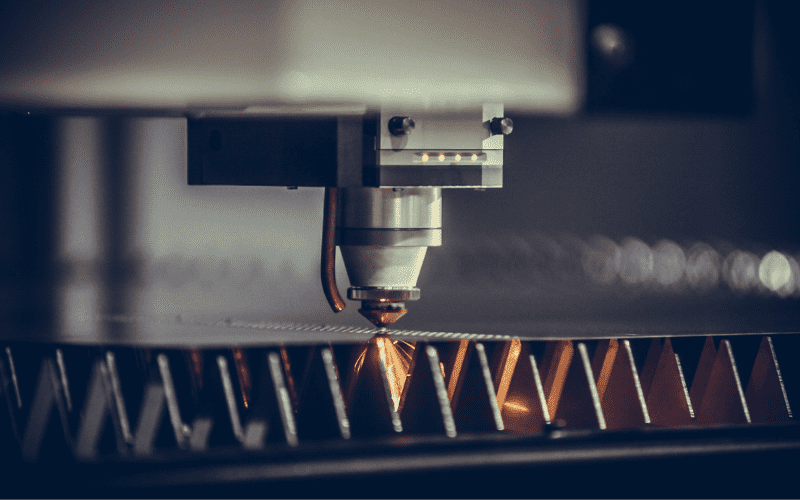
One unique characteristic of laser cutting that sets it apart from other cutting techniques is precision. It can be cut to as small as 0.006 of an inch. This is useful when working with intricate designs, you want to etch or engrave. The precision of laser cutting can cut almost seamlessly onto the material.
As mentioned, etching and engraving are one facet of laser cutting that is not viable with water jet cutting. Etching and engraving with laser beams allow you to offer additional services to clients more than just cutting. With this, you can put in some designs on a material. You can even engrave assembly marks like serial numbers to materials before or after cutting.
One thing to watch for with laser cutting is wearing safety goggles. This will help protect you from smoke and, sometimes, dust. Ventilation is also ideal with a laser-cutting process. This is because some metals, especially plastic materials, emit toxic fumes when exposed to laser beams. Although the risk is relatively low compared to water jet cutting, cleanup is much easier.
What is water jet cutting?
Since water-cutting techniques use highly pressurized water to cut through materials, using as high as 60,000 PSI (pounds per square inch) of power is not uncommon. Water cutting is almost an ideal option for various types of material you need to cut. And the abrasives added to the process make the turnaround time much faster.
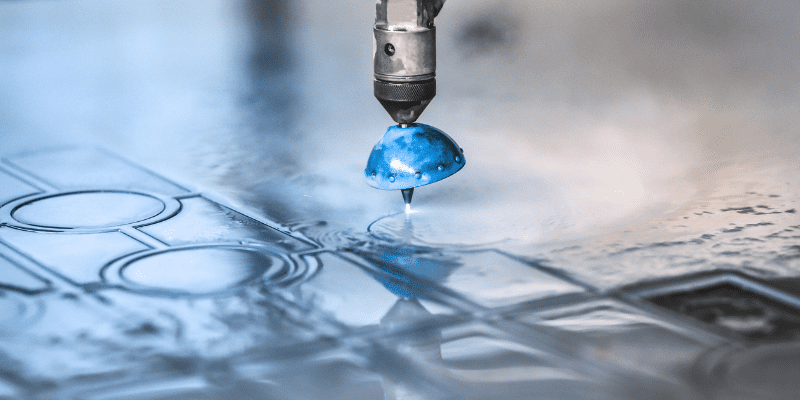
More than just a quicker cutting time, these abrasives also lend a hand in replicating the natural erosion process in nature. Water cutting mixed with abrasives can mimic the same result, and look if you have seen how water carves out riverbeds and even cliffs.
One thing you need to realize with water cutting is the need for a larger space. Water-cutting equipment tends to have more pieces than laser-cutting, where the laser beam is already inside the machine. The pump needed for the water is a separate piece of equipment from the cutter itself. This means you need more space for the whole process to work.
How are they different?
Now that you know how laser and water jet cutting work, they have much more to offer. This is where you begin understanding each technique’s pros and cons.
Process
The most obvious difference between the two is the technique used in cutting. High-pressure water is used in water cutting, while laser beams are used in laser cutting.
Safety & Cleaning
In every cutting job, you always need to prioritize the safety of the operators as well as a clean production area. And when it comes to both, wearing safety goggles is always best. Laser cutting can protect your eyes from smoke and dust. But goggles can protect your eyes and face from abrasive materials in water jet cutting. Ear protection is also necessary for water jet cutting since the process is very noisy.
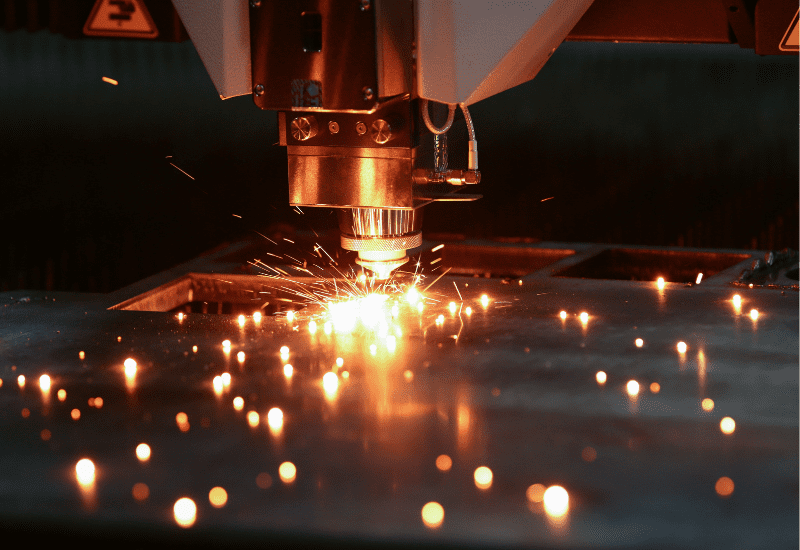
When cleaning up, you most need good ventilation in laser cutting. This helps toxic fumes to air out into the open. But with water jet cutting, the abrasive and water left over from the cutting process require extensive cleaning.
Thickness and cutting precision
The laser cutting technique works best with at least 3mm to 10mm materials. But when it comes to a water jet, it can go from 10mm to 50mm. One thing to remember is that cutting thinner materials with a water jet might not be a good idea. This is because the high pressure of the water could damage the thin material while cutting.
Regarding cutting precision, lasers can be as small as an average of 0.006 inches. This is a lot more precise when compared with the 0.5mm or 0.02 inches of water jet cutting.
What are the benefits of each
One aesthetic benefit of laser cutting is that it can leave burn marks on some materials. Although most can be removed by cleaning, it can be used in the overall design for some engraving or etching projects. This technique is better when you need precision cuts and put assembly marks on the material you are working on.
There are even some industries that prefer one over the other. For laser cutting, here are a few of them.
- Automotive – floor pans and roos and even interior engraving.
- Jewelry – the precision of laser beams makes it ideal for cutting precious jewelry with minimal wastage.
- Medical – more than making high-quality devices like valves and stents, the laser also lends a hand to doctors and allows them to operate precisely.
The sheer power of water jet cutting makes it a viable option for most materials. You can work on almost any type of material and cut them. For water jet cutting, here are industries that use them.
- Automotive can work on high-thickness areas like metal gaskets and custom bodies.
- Aerospace – the absence of heat makes cutting engines and turbine blades ideal since it does not lead to warping or small cracks.
Cost comparison between water jet cutter and laser cutter?
You must also factor in production speed, where laser cutting is better than water jet cutting. This gives you an idea of how many projects you can finish in a given time. Of course, you need to factor in the type of material and thickness to determine which is better.
Laser cutting comes out on top when considering other factors in the cost comparison, like power costs, maintenance, consumables, gases, and even abrasive materials. The average cost for laser cutting could be as low as $2/hour. You could be looking at $30/hour just to run it for water jet cutting.
Regarding component costs, laser-cutting machines average down to a low number since there is a demand for the process. However, water jet cutting has a higher cost for components. There are consumables like abrasives and water and high machine maintenance.
What materials can be cut with a water jet than a laser cutter?
This is one of the key differences between laser cutting and water jets. Though there are overlaps in the types of materials they can work on, each has specific pros and cons. Overall, a water jet has almost no restrictions on the type of material it can cut. Since it does not produce heat, it can go through almost anything.
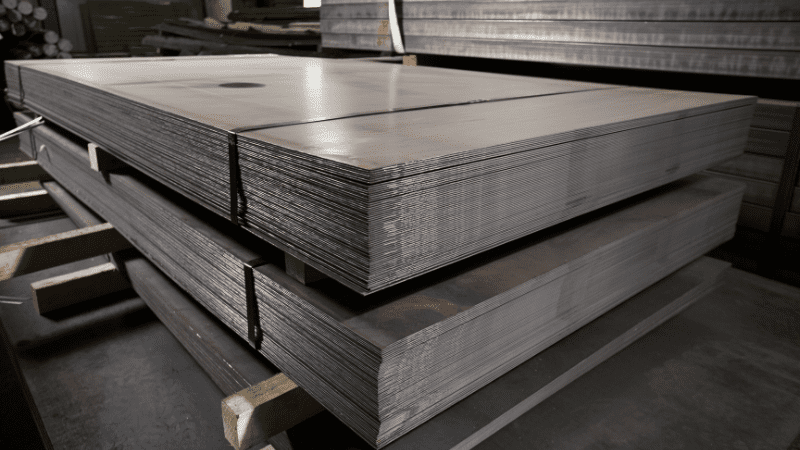
On the other hand, many materials still use laser cutting, but some restrictions exist. For one, reflective materials are a challenge for laser-cutting machines. It can reflect the laser beam and bounce off the material. Thermolabile products will not work well with laser cutting, well. These substances decompose when subjected to extreme heat, such as 55℃ or more.
Here are some specific materials that each cutting technique can work on:
Laser Cutting | Water Jet | |
Metal | Aluminum, Brass, Carbon Steel, Copper, Stainless Steel, Titanium | |
Hardox, Tool Steel, Copper, Mild Steel | ||
Composites | Aero Fiber, Carbon Fiber, Fiberglass, Kevlar | |
Naturals | Wood, Paper, Leather, Cardboard, Cork | Ceramic, Quartz, Granite, Marble, Cement, Man-made stone |
Plastics & Rubber | PVC, Foam, Rubber | Foam, Rubber, PVC, |
Acrylic, Polycarbonate, Silicone | ||
Miscellaneous | Food, Insulation Materials, ISO wall |
Which one is better for you?
The best cutting technique depends on what you are working on and the output you are looking for. Each cutting technique has pros and cons; taking those in is a good idea to determine the best option for the job.
Both cutting techniques, to some extent, cause damage to the material they are cutting. The manufacturing process is not perfect, and it even has limitations. This is important in helping you determine if you will use laser cutting or water jet cutting.
Water jet cutting is your best option for working on thick materials. You have to bear in mind that it would not be a small and precise cut. Add the fact that the abrasives added to the water normally end up with an “eroded” effect on the material after the cutting process.
However, you can opt for laser-cutting if you are working on thin and even delicate materials. It offers a more precise cut which is crucial, especially in the jewelry and medical field. Doctors even use lasers to make precise cuts during delicate operating procedures.
Water jet cutting can also work in delicate industries for different reasons. For example, the aerospace industry. Experts in this field prefer the cutting process of a water jet not only because they usually work with thick materials.
But more importantly, the absence of heat makes it ideal for lowering the chances of small cracks or even warping in the materials they are cutting. These are valid concerns since these defects can significantly affect and damage their end products. Planes, jets, and even space shuttles travel at incredible speeds. A small crack or warp in their components can result in significant problems down the line.
FAQS
- Is water jet cutting better than laser?
Water jet cutting is better than laser cutting thick materials that cannot be exposed to heat. A laser is a much better option if working with thin materials requiring precision cuts.
- What advantages does water jet cutting have over cutting methods?
Water jet cutting is better for cutting a wider range of materials than laser and other techniques. The absence of heat makes it an ideal option when cutting materials for sensitive industries like aerospace and automotive. Including an abrasive during the cutting process also gives the effect of naturally eroding edges.
- Is water jet cutting accurate?
Water jet cutting is accurate, but laser cutting can be more precise. The smallest cut a water jet can make is at 0.02″. On the other hand, laser cutting can make cuts as accurate as 0.006 of an inch.
- Why is not a water jet a popular choice for cutting metal?
Although water jets can cut through most metals, some industries prefer laser cutting. The most common reason is the accuracy of the cut. The more precise the cut, the fewer parts of the material go to waste. There are also production options with a laser, such as assembly marks on the material, like serial numbers.
Conclusion
Laser and water jet cutting are the most preferred cutting techniques across several industries worldwide. Now that you have an idea about the advantages and downsides of each, you can make a good decision about which one to choose. But there is a better way of doing it–Choose Baison to help you!
Baison Guides You For Free
We are (Baison) proud of ourselves in some of the top experts in laser cutting and other techniques. As a result, we have worked with countless companies spanning several industries delivering quality output every time.
We can help and guide you as you decide which cutting technique suits your needs. Our field and industry experts are ready to talk to you at present!